Introduction
Fastener nuts are integral to a wide range of industries. These key components play a crucial role in mechanical assemblies by securely holding parts together. Whether you’re working with hex nuts, lock nuts, or castle nuts, understanding the manufacturing process of these fasteners will enable you to make informed and effective procurement decisions. In this article, we will explore the entire nut manufacturing process, from material selection to forging, machining, heat treatment, surface treatment, and quality control.
By the end of this guide, you will have a comprehensive understanding of the various types of nuts and the detailed steps involved in producing a high-quality fastener nut.
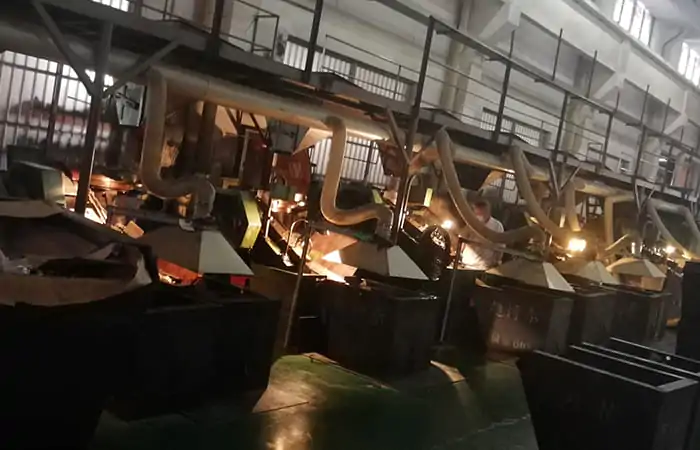
1. Material Selection: Choosing the Right Material for Nuts
The first step in manufacturing fastener nuts is selecting the right material. The material chosen plays a vital role in determining the nut’s strength, durability, and resistance to environmental factors like corrosion. Common materials used for making nuts include:
- Carbon Steel: This is the most commonly used material for fastener nuts. It offers a good balance of strength and cost-effectiveness, making it ideal for general-purpose applications.
- Stainless Steel: Ideal for environments where the nut will be exposed to moisture or chemicals. Stainless steel provides excellent corrosion resistance and is often used in the automotive and construction industries.
- Alloy Steel: Known for its enhanced strength and resistance to high temperatures, alloy steel is used for heavy-duty applications where high strength is crucial, such as in the aerospace or energy sectors.
2. Forging: Shaping the Nut with Heat and Pressure
Once the material has been selected, we proceed with the next stage: forging. This process involves heating the material to a high temperature and shaping it under significant pressure. It is an essential step in the manufacturing of the nut’s basic structure. Not only does forging form the foundation of the product, but it also strengthens the material, improving its mechanical properties, such as durability and strength.
The advantages of forging nuts include:
- Improved Strength: The high pressure used in forging compacts the material’s grain structure, resulting in a stronger and more durable nut.
- Consistency: Forging ensures that each nut has consistent material properties, reducing the likelihood of defects.
- Reduced Waste: Compared to other processes, forging tends to generate less waste, making it a cost-effective manufacturing option.
3. Machining: Refining the Threads
After forging the nut, it progresses to the machining phase. During this critical stage, the nut is meticulously refined to ensure it meets the precise specifications needed for its intended application.
The machining process is primarily focused on the creation of internal threads, which are essential for the proper function of the nut when paired with bolts or screws. There are two key methods for producing these threads:
- Cutting Threads: This method involves using a die to cut the internal threads directly into the nut.
- Thread Rolling: In this process, the nut is passed between hardened rollers that form the threads without removing material, which can increase the nut’s strength.
Precision in machining is crucial, as the quality of the threads determines how well the nut will fit and function with bolts or studs.
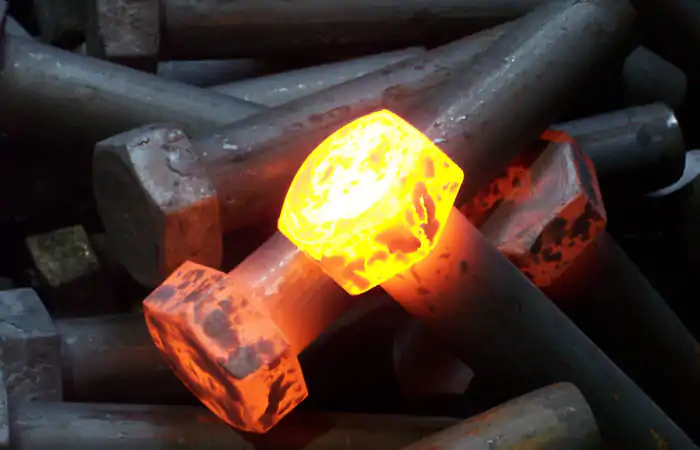
4. Heat Treatment: Strengthening the Nut
To enhance the strength and hardness of the nut, heat treatment is commonly used. This process involves heating the nut to high temperatures and cooling it at a controlled rate, ensuring the desired properties are achieved effectively.
Common heat treatment methods for nuts include:
- Quenching: The nut is heated to a high temperature and then rapidly cooled, which increases hardness.
- Tempering: After quenching, the nut is reheated to a lower temperature and then cooled slowly. This process reduces brittleness while maintaining high strength.
Heat treatment ensures that the nut can withstand heavy loads, harsh environments, and wear over time.
5. Surface Treatment: Improving Durability and Corrosion Resistance
One of the final steps in manufacturing fastener nuts is surface treatment, which is essential for improving the nut’s durability, corrosion resistance, and appearance. There are several common surface treatments used for nuts:
- Galvanizing: This involves coating the nut with a layer of zinc, which protects it from rust and corrosion, making it ideal for outdoor or marine applications.
- Black Oxide Coating: A process where the nut is coated with a black oxide layer to enhance corrosion resistance and provide an aesthetically appealing finish.
- Coatings: Special coatings, such as polyester or other polymers, may be applied to the nut for additional protection against wear and environmental factors.
These surface treatments ensure that the nut can maintain its functionality and appearance even under challenging conditions.
6. Quality Control: Ensuring the Nut Meets Industry Standards
Quality control plays a pivotal role in the nut manufacturing process. To guarantee that each nut adheres to the necessary specifications and performs reliably in its designated application, comprehensive and stringent quality control tests are executed throughout the production stages.
Key quality control procedures include:
- Dimensional Checks: The nuts are measured to ensure they meet the exact size and thread specifications.
- Tensile Strength Testing: The nuts are tested to ensure they can withstand the specified loads without failing.
- Corrosion Resistance Testing: This involves testing the nuts in different environments to ensure that the surface treatments are effective at preventing corrosion.
Nuts that pass these tests are certified to meet industry standards like ISO or DIN, ensuring that they are safe and reliable for use in critical applications.
7. Types of Nuts: Exploring Popular Nut Types
Fastener nuts come in various shapes and sizes, each designed for specific applications. Here are some of the most common types of nuts used in different industries:
- Hex Nuts: The most common type of nut, characterized by a six-sided shape. Hex nuts are widely used in construction, automotive, and machinery applications.
- Lock Nuts: These nuts are designed to resist loosening due to vibrations. They are typically used in high-vibration environments such as in automotive and industrial applications.
- Castle Nuts: These nuts have a unique design with slots that allow them to be secured with a cotter pin, preventing them from loosening. They are commonly used in automotive and heavy machinery applications.
FAQ: Common Questions About Fastener Nuts
1. What is a fastener nut?
Nuts are fasteners with threaded holes that secure to bolts, screws, or studs, holding parts together and preventing axial movement.
2. What is a nut material?
Nuts are commonly made from materials like carbon steel, stainless steel, and alloy steel. The material chosen depends on the specific application requirements such as strength, durability, and resistance to corrosion.
3. What is the difference between a bolt and a nut?
A bolt is a type of fastener with an external thread, whereas a nut has an internal thread and is used to secure the bolt in place. The bolt and nut work together to hold two or more objects together.
Conclusion
Understanding how fastener nuts are made provides us with a greater appreciation for the skill and precision involved in crafting these critical components. Whether you’re looking for hex nuts, lock nuts, or castle nuts, knowing the processes involved—from material selection to forging, machining, and quality control—helps ensure you choose the right fastener for your specific requirements. Should you have any questions or want further insights into the manufacturing process, don’t hesitate to get in touch!
Contact Hengrui Fastener for Custom Nut
For specialized applications that require custom solutions, Hengrui Fastener offers high-quality, customizable nuts fasteners. Whether you need a specific size, material, or finish, Hengrui can provide tailored fasteners to meet your exact requirements. Visit Hengrui Fastener to learn more about our products and services.