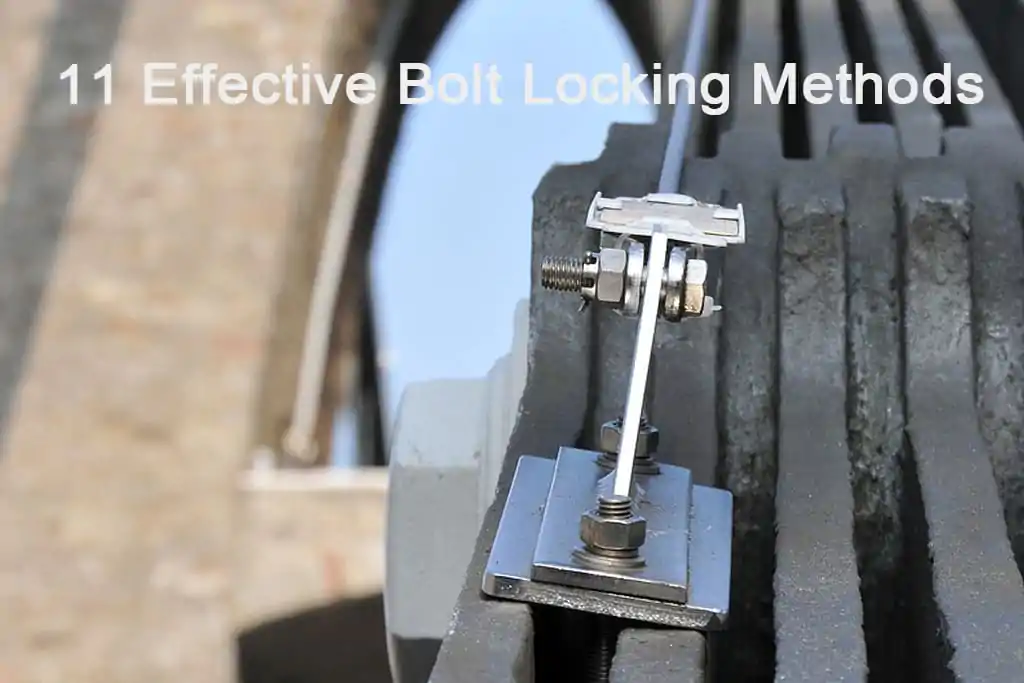
Why bolt locking is important?
Choosing the correct locking method is crucial to ensuring the safety and reliability of bolted connections. Loose bolts can cause danger and accidents. From industrial machinery to automotive applications, effective bolt locking prevents mechanical failure and extends component life. As a nut and bolt supplier, with this guide we’ll explore how to lock a bolt in place and understand their advantages.
What are the factors that affect bolt locking?
Several factors can affect the effectiveness of bolt locking methods:
- Vibration: Continuous movement can cause bolts to loosen, so effective locking is critical.
- Environmental Factors: Corrosion, temperature changes, and exposure to chemicals can reduce the performance of locking structures.
- Load Fluctuations: If not secured, changes in load may cause the bolts to loosen.
11 Types of Bolt Locking Methods
Bolt locking methods can be divided into three types: friction locking, mechanical locking and permanent locking. Each meets unique application needs and environments.
1. Friction Locking Methods
Friction locking employs resistance between threads to prevent loosening due to vibration or rotational forces. Common friction locking methods include:
- Spring Washer: Employs elastic force to maintain preload and tension.
- Advantages: Simple, inexpensive, reusable.
- Disadvantages: Less effective under dynamic loads; can lose tension over time.
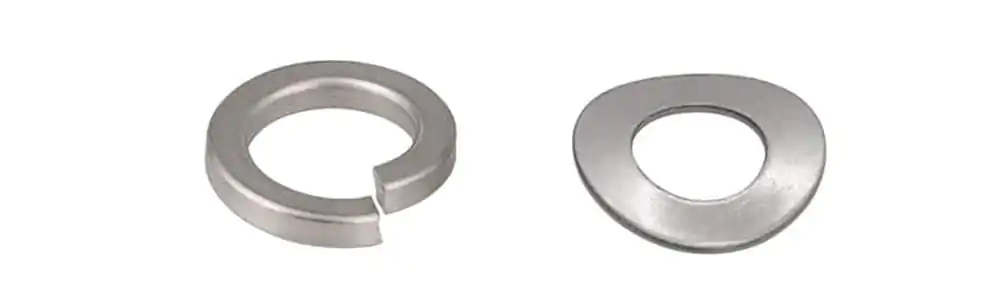
- Lock Washer(such as Wedge-locking Washers, Tooth lock washers): A lock washer is placed directly between the fastening element (bolt head or nut) and the surface of the material being secured, has a split to provide a spring force and exert pressure, effectively prevent loosening due to vibration or movement.
- Advantages: Provides good resistance to rotation.
- Disadvantages: Can cause damage to the contact surface; not ideal for critical applications.
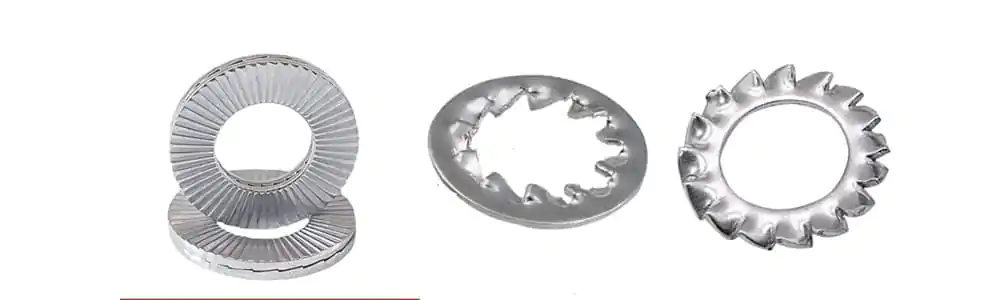
- Nylon Insert Nut (Nyloc Nut): A nylon insert nut contains a nylon collar or ring at the top of the nut. When installed, the bolt threads have to forcefully engage with this nylon ring, which deforms slightly to conform to the threads. This deformation causes a significant increase in friction between the nut and the bolt, preventing accidental loosening.
- Advantages: Excellent resistance to vibration, can be reused a few times.
- Disadvantages: Not suitable for high temperatures; plastic insert may degrade.
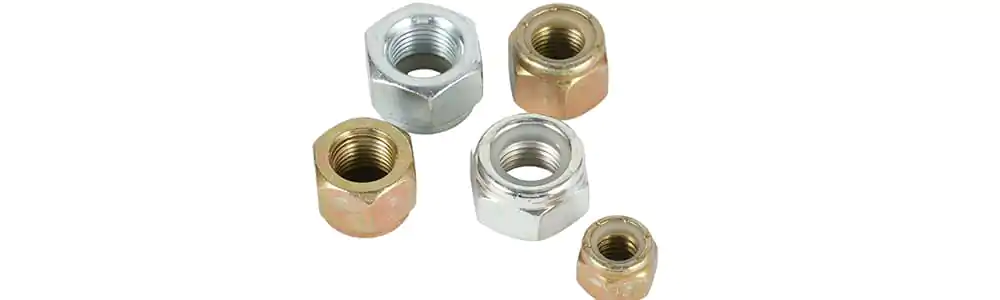
- Keps K-Lock nut(Lock Nut): Keps K-Lock nuts come with pre-installed free-turning external tooth lock washers to prevent loosening by increasing friction.
- Advantages: Quick to install, reusable, and provides good vibration and anti-shake effects.
- Disadvantages: Cost is higher and may not be as effective as chemical or welding methods in locking against extreme vibration and loads.
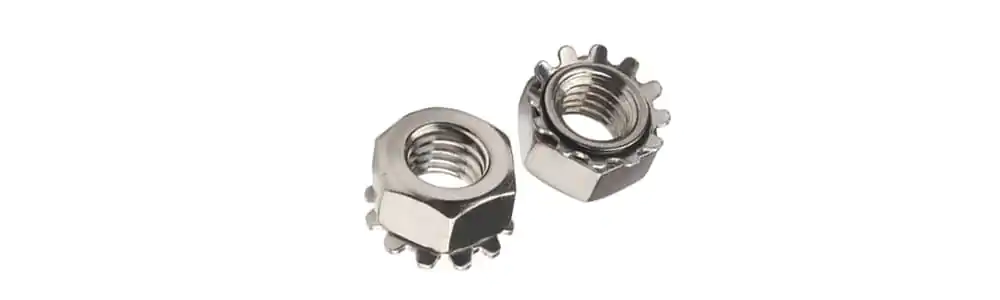
- Hex Flange Nut with serration(Lock Nut): The bottom of this nut has a serrated flange. When installed, the serrations bite tightly into the connected material and prevent loosening through friction.
- Advantages: Quick installation, no additional parts required, enhanced vibration resistance.
- Disadvantages: May damage the connected surface, poor reusability.
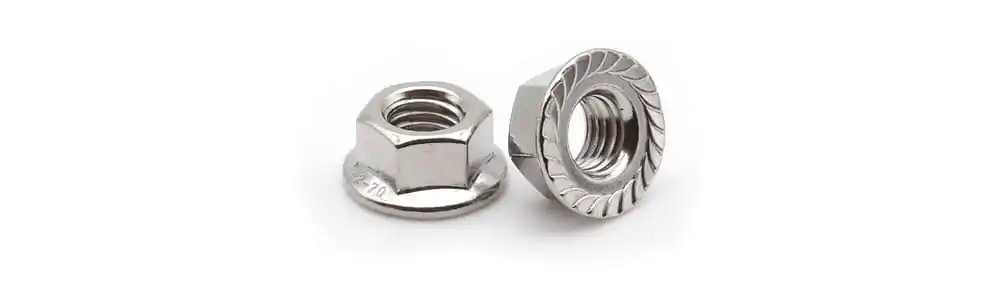
- Self-Locking Nut: Designed with a distorted thread in the nut to create an increased friction.
- Advantages: Maintains preload well, multiple types available.
- Disadvantages: Often more expensive than standard nuts; can be difficult to install and remove.
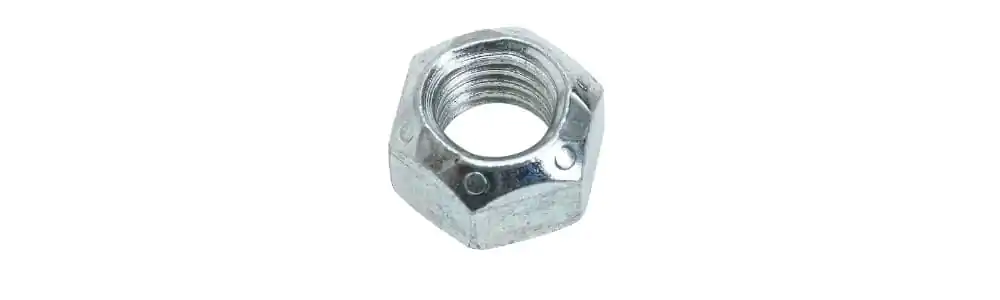
- Double Nutting (Jam Nut ): Using two nuts tightening against each other, the inner nut is torqued first, followed by the outer nut which is tightened against the first. This creates a clamping force between the two nuts themselves, rather than the bolt and the installation material, effectively locking the bolt in place through increased friction.
- Advantages: Effective at preventing loosening by creating a locking action through the tension of two nuts.
- Disadvantages: Requires precise torque control; takes up more space on the bolt.
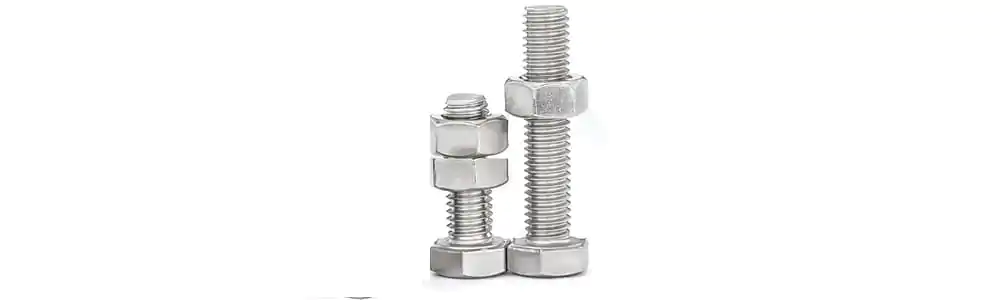
These methods all enhance the friction between the bolt and nut interface, significantly reducing the possibility of loosening under vibration.
2. Mechanical Locking Methods
Mechanical methods involve adding a physical mechanism to maintain bolt tension and prevent loosening, such as:
- Tab Washers: A washer with tabs that bend over the nut or bolt head providing a lock against rotation.
- Advantages: Simple to apply; effective against loosening due to vibrations.
- Disadvantages: Can make disassembly difficult; chemical resistance varies.
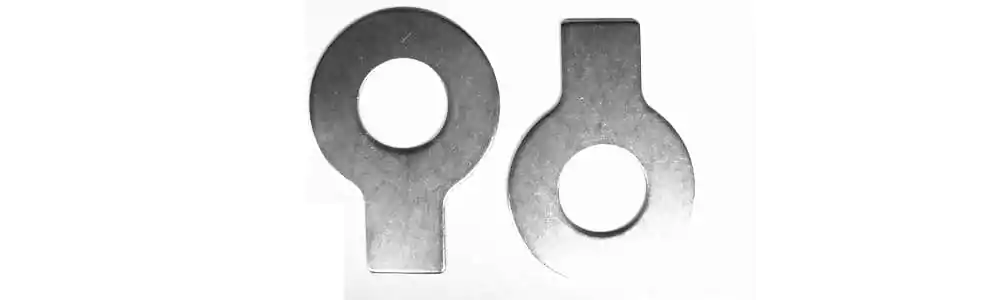
- Safety Wire or Cotter Pins: Used in aerospace to prevent critical component loosening.
- Advantages: Provides a physical barrier to nut rotation; reliable in safety-critical applications.
- Disadvantages: Time-consuming to install; not reusable.
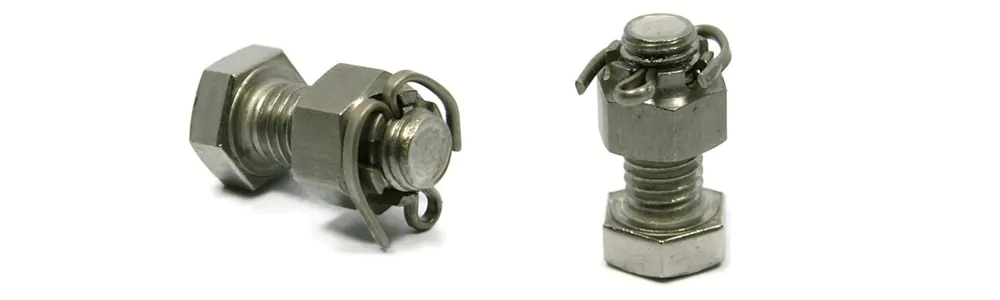
These methods are generally more robust than friction methods and are used in applications where failure of the bolted joint is not an option.
3. Permanent Locking Methods
Permanent methods like welding, adhesive bonding, or peening involve altering the physical characteristics of the bolt assembly. Common approaches include:
- Welding: Bolts are welded to the assembly, permanently locking them in place.
- Advantages: Provides a permanent solution; very strong.
- Disadvantages: Destroys the integrity of the bolt; not suitable for all materials.
- Adhesives or Thread-locking Fluids: Chemical adhesives applied to bolt threads that harden.
- Advantages: Applying threadlocker is simple and cost-effective
- Disadvantages: Difficult to disassemble, often resulting in damaged fasteners
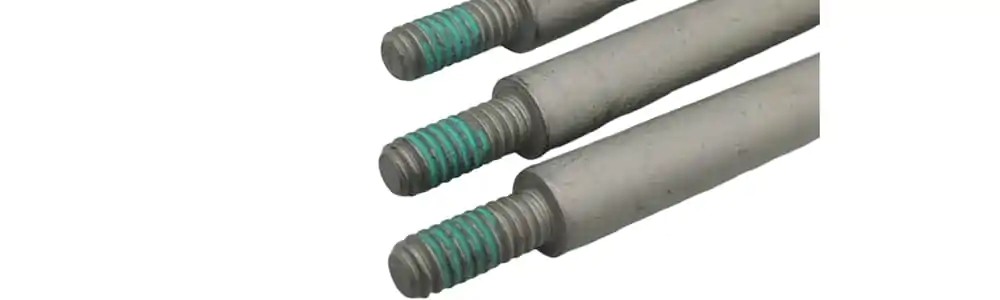
These are used in non-serviceable situations where the bolted joint is not intended to be disassembled.
How to selecting the Right Bolt Locking Method?
Choosing the right bolt locking method depends on several factors including the application environment, load conditions, and maintenance requirements. Here’s how to select the appropriate method:
- The Application scenes: Consider the operational environment (temperature, vibration, load). For high-vibration environments, mechanical locking methods may be more suitable.
- Consider the Load: Higher loads may need a stronger locking mechanism, such as a double nut or mechanical device.
- Maintenance and Reusability: Determine if the bolt will need to be removed or adjusted frequently. Reusable options like nylon insert nuts are beneficial for assemblies that require regular maintenance.