Are you working on a project that demands a reliable, versatile fastener? Perhaps you’re finding it challenging to choose the right screw for the job. If you’re nodding your head, then you’re in the right place. Let’s dive deep into the world of pan head screws and why they might be exactly what you need.
What is a Pan Head Screw?
A pan head screw is a type of threaded fastener distinguished by its unique mushroom-like head, resembling the bottom of a flipped frying pan. This design serves a very functional purpose. The head is wide, round, and flat on the underside, which helps to distribute pressure evenly across the surface it fastens.
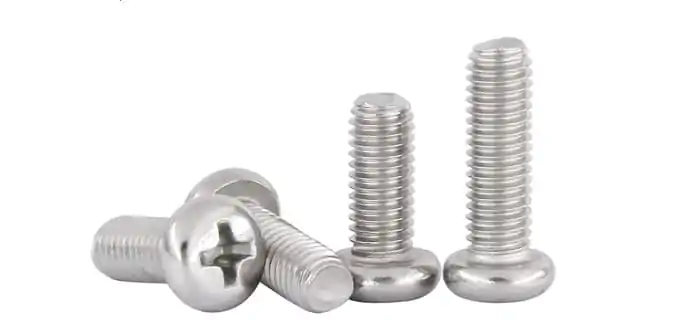
Pan head screws are available in various sizes and materials, making them adaptable for different applications. They’re also compatible with several drive types, including slotted and Phillips, which adds to their versatility.
What Are Pan Head Screws Used For?
Pan head screws are incredibly versatile, which is why they are found in a wide range of industries. Their unique design offers both functional and aesthetic benefits, making them the go-to fastener for many professionals.
Electronics: In the electronics industry, pan head screws are often used to secure circuit boards and other electrical components. The non-countersunk design provides ample support and distributes the load evenly, which is crucial when working with delicate electronics.
Machinery and Equipment: In mechanical assemblies, pan head screws are perfect for fastening parts that may be subject to vibration. The broad, flat head provides stability and helps maintain a secure connection, even in dynamic environments.
Cabinetry and Carpentry: In woodworking, pan head screws are commonly used to attach hardware such as drawer handles and hinges. The non-countersunk head offers a firm grip while ensuring a clean appearance, reducing the risk of snagging.
Automotive Industry: In the automotive world, pan head screws are frequently employed to secure trim pieces and panels. Their design not only provides a strong hold but also contributes to a sleek, unobtrusive finish.
Metal Construction: In metalworking, these screws are used to fasten metal panels to frames, ensuring a secure connection. The wider surface area prevents damage to the metal being fastened, and many are self-tapping, eliminating the need for pre-drilled holes.
What is the Advantage of a Pan Head Screw?
The main advantage of a pan head screw lies in its ability to distribute the load evenly across the surface it secures. This feature brings several benefits:
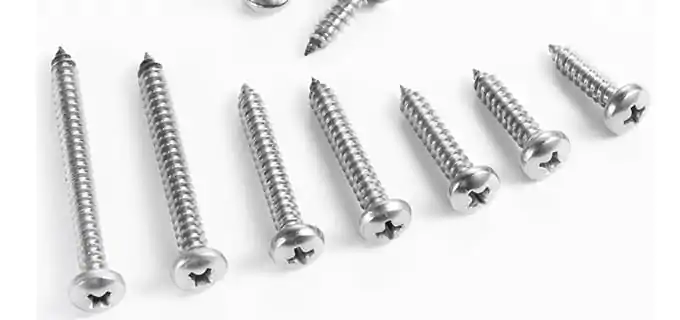
Even Load Distribution: The wide, flat head of a pan head screw allows it to spread the applied force over a larger area compared to other types of screws. This helps prevent damage or deformation of the material being fastened, which is particularly important when working with delicate or thin materials.
Provides Stability: The broad bearing surface of the pan head ensures a stable connection, especially in applications where the fastened parts might be subjected to vibrations or movements. This stability helps maintain a secure joint over time.
Minimized Protrusion: While the pan head does not sit completely flush with the surface, its low-profile design minimizes protrusion. This contributes to a more aesthetically pleasing finish and reduces the chances of the screw head catching on other objects.
Versatility in Application: The load distribution feature and low-profile design make pan head screws suitable for a wide range of applications across various industries. They are frequently used in electronics, mechanical equipment, carpentry, automotive, and metal construction.
Ease of Installation: Pan head screws are compatible with a variety of screwdrivers, such as slotted, Phillips, or hex. This versatility makes them easy to install for most users, even in challenging situations.
How Are Pan Head Screws Measured?
When selecting a pan head screw, it’s essential to understand the key dimensions that determine its suitability for your application. Pan head screws are typically measured by several critical parameters:
Diameter: This refers to the basic diameter of the screw shaft and is usually expressed in inches or millimeters.
Head Diameter: The diameter of the pan head itself, which is wider than the shaft. This measurement is vital to ensure the screw fits properly in the intended application.
Head Height: This measures the vertical height of the head from the base to the top. It affects how much clearance is needed when installing the screw.
Head Radius: The radius of the rounded top of the head contributes to the screw’s overall shape and aesthetic.
Slot Width and Depth: For slotted head screws, these dimensions indicate the width and depth of the slot that accommodates the screwdriver.
Size Standards: Pan head screws are often categorized by size numbers (e.g., #4, #8, #10) or specific dimensions (e.g., 1/4″, 3/8″). The American National Standards Institute (ANSI) provides specifications for these sizes to ensure compatibility and performance in various applications.
What is the Difference Between Pan Head and Round Head Machine Screws?
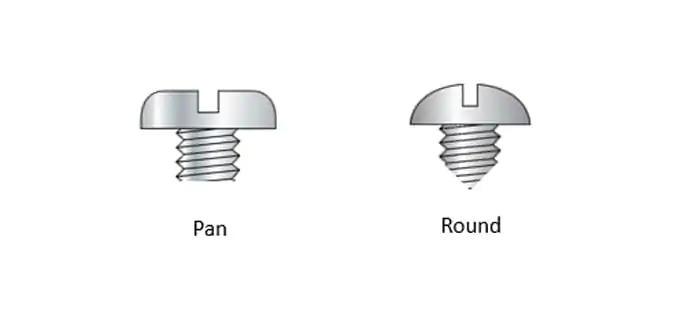
At first glance, pan head screws and round head machine screws may seem similar, but they have distinct differences that set them apart.
Head Shape: Pan head screws have a round head with a flat bearing surface and a slightly domed top. When viewed from the side, they have a trapezoidal shape, offering more surface area for load distribution. Round head machine screws, on the other hand, have a fully rounded, semi-spherical head. The sides of the head are more dome-like compared to pan head screws, leading to greater protrusion when installed.
Slot Type: Pan head screws come in various slot types, including slotted and Phillips, providing versatility for driving tools. Round head machine screws typically have only a slotted head, limiting the choice of driving tools.
Load Distribution: The flat bearing surface of pan head screws offers better load distribution, making them suitable for applications involving softer materials or requiring a firm grip. While round head screws provide good holding power, their round shape may not distribute load as evenly, particularly in softer materials.
How Do You Remove a Pan Head Screw?
Removing a pan head screw is usually straight forward, but there are a few tips to make the process even smoother:
Use the Correct Screwdriver: Ensure you’re using the appropriate screwdriver for the job. For slotted pan head screws, use a flathead screwdriver. For Phillips pan heads, use a Phillips head screwdriver. This will give you the best leverage and minimize the risk of damaging the screw head.
Apply Penetrating Oil: If the screw is stuck or rusted, spray some penetrating oil like WD-40 into the screw head slot. Let it sit for a few minutes to work its way into the threads. This can help break the bond and allow the screw to turn more easily.
Use a Screw Extractor: If the screw head is stripped and a screwdriver won’t grip, you can try using a screw extractor. This tool has reverse-threaded flutes that bite into the screw when turned counterclockwise. Drill a pilot hole into the screw head, then screw the extractor in to back the screw out.
Grind Off the Head: As a last resort, you can use a rotary tool with a cut-off wheel to grind off the screw head. This exposes the threads so you can unscrew the remainder with pliers or vice grips. Be careful not to damage the surrounding material when grinding.
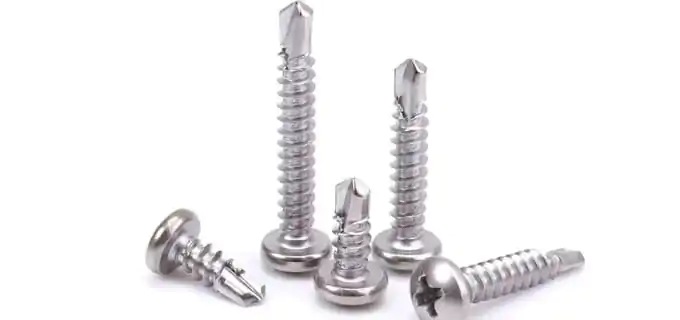
Choosing the Right Pan Head Screw?
Selecting the right pan head screw for your project involves considering several key factors to ensure the best fit and performance:
Material: Choose a screw material based on the environment and application. For outdoor or corrosive environments, stainless steel is ideal due to its resistance to rust and corrosion. For decorative applications, brass may be more suitable.
Thread Pattern: The thread pattern should match the materials being fastened:
- Coarse threads are best for softer materials like wood, providing better grip.
- Fine threads work well with harder materials such as metal or plastic, offering a tighter hold.
Screw Length and Diameter: The length and diameter of the screw should match the thickness of the materials being fastened and the load capacity required. Measure from where the head sits flush against the surface to the tip of the threaded part to determine the correct length.
Driving Tool: Ensure you have the right driving tool for the screw head type. Pan head screws can have various head types, including slotted, Phillips, and hex. A drill is effective for driving Phillips, Torx, and Hex head screws, while slotted screws may require more care to avoid slipping.
Conclusion
So there you have it—a comprehensive guide to pan head screws. From understanding their design to choosing the right one for your project, I hope this guide has shed some light on these versatile fasteners. Whether you’re in electronics, construction, or just a DIY enthusiast, pan head screws are your go-to solution for reliable, durable fastening.
Feel free to reach out to us at Shanghai Hengrui Industry Co., Ltd for any of your pan head screws needs. We are here to help you find the perfect solution for your applications.