Looking for a simple way to make fastening tasks easier? Self-tapping screws are the answer. They create their own threads as they go in, so you don’t need to pre-drill holes. This saves time and effort. With a strong grip and easy installation, self-tapping screws are perfect for any project.
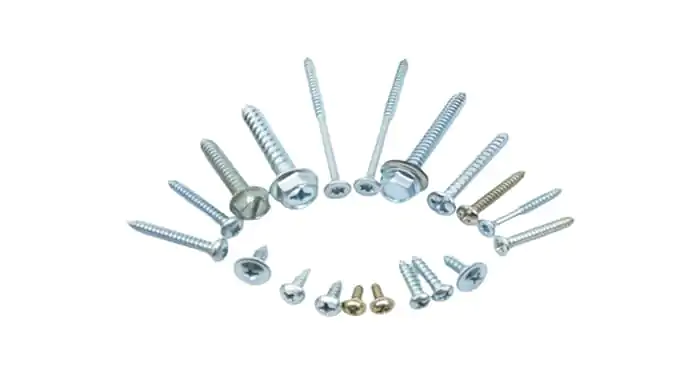
What Is A Self Tapping Screw?
A self-tapping screw is a fastener that makes its own hole as it’s driven into a material. These screws are incredibly efficient, saving time and effort in many tasks. They can create their own threads in materials like wood, plastic, and metal, eliminating the need for pre-drilling holes.
Self-tapping screws have different designs for different uses. Sharp tips make them ideal for softer materials like wood, while blunt tips are used with pilot holes in harder materials like metal. They also come in various head styles, such as pan, flat, and hex heads, to fit different needs.
Even though self-tapping screws can create their own threads, drilling a pilot hole can make installation easier, especially in hard materials. It also helps prevent damage to the material. Avoid over-tightening to maintain the screw’s hold. Proper alignment is key to a secure fit.
Self-tapping screws come with different tail types, including A, AB, B, BP, BF, and BT. The AB type is popular because it’s versatile and easy to use, making it suitable for many applications.
Types of Self-Tapping Screws
Thread-Forming Screws: Thread-forming screws displace the material around them rather than cutting it, This makes self-tapping screws perfect for softer materials like plastic and thin metals. Since they don’t remove material, they keep the material strong and provide a secure hold.
Thread-Cutting Screws: Unlike thread-forming screws, thread-cutting screws have cutting edges that remove material to create threads. They can be used with many materials, such as wood and metal. However, you need to be careful during installation to avoid stripping the threads.
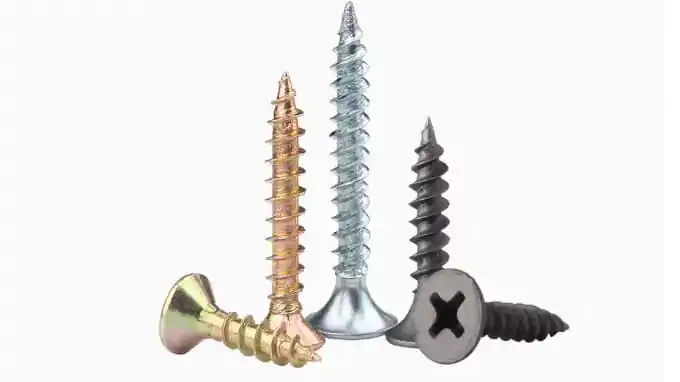
The Material of Self Tapping Screws
Self-tapping screws are typically made from durable materials to withstand various environmental conditions and applications:
- Carbon Steel Self tapping screws: Carbon steel is a common choice, providing strength and durability. Steel screws are often coated with zinc or phosphate to resist corrosion.
- Stainless Steel Self tapping screws: Stainless steel screws resist rust, making them great for use outdoors or in wet areas. The nickel and chromium in stainless steel make it strong and help prevent corrosion.
- Brass and Aluminum Self tapping screws: Brass and aluminum are less common materials for screws but still useful in certain cases. Brass screws look nice and resist rust, making them good for decorative projects. Aluminum screws are light and resist rust as well, but they aren’t as strong as steel screws.
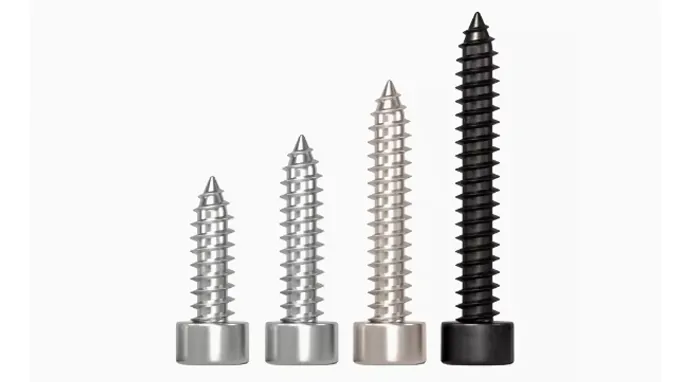
Self-Tapping Screws Drive Types
Self-tapping screws come in various drive types, each suited for specific applications and tools. Here are some of the most common ones:
- Phillips Drive
- Square Drive (Robertson)
- Torx Drive
- Hex Drive
- Slotted Drive
The Purpose of Carburizing in Self-Tapping Screws
Carburizing is used to make the surface of self-tapping screws harder, which helps make the threads stronger. If there is too much decarburization or not enough carburization, the threads might not be strong enough. This can cause the threads to get damaged during use.
Mechanical Properties Requirements for Self-Tapping Screws
- Core Hardness: Standard value is HRC 28-38.
- Surface Hardness: Standard value is MIN HV450.
- Carburized Layer Depth:
- For #4-6: 0.05-0.18 mm
- For #8-12: 0.10-0.23 mm
- For #14: 0.13-0.28 mm
These standards ensure that the screws are durable and perform effectively in various applications.
What Are the Advantages and disadvantages of Self-Tapping Screws?
Self-tapping screws are a popular choice because they are easy to install. Since they don’t need pre-drilling, you can save a lot of time, especially in fast-paced environments. This makes them ideal for projects where efficiency is key.
These screws are designed to go in smoothly and create their own threads, giving you a strong and secure hold without needing too much force. This makes them suitable for various materials and applications.
Made from strong materials, self-tapping screws are built to last. They resist wear and corrosion, making them perfect for many uses, from construction to automotive work.
While self-tapping screws offer many benefits, they do have some disadvantages. One main drawback is the risk of over-tightening, which can strip the threads and weaken the connection. Additionally, repeated use of self-tapping screws in the same hole can wear out the material, leading to a loose fit over time. This can be a concern in applications where strong and durable connections are critical.
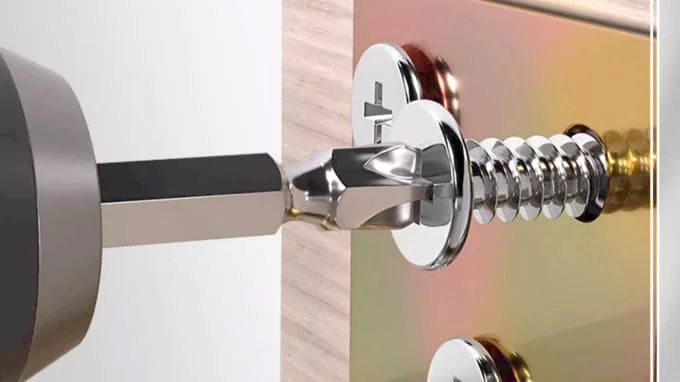
What Is the Use of Self-Tapping Screws?
Self-tapping screws are versatile and can be used for:
- Joining Different Materials: They are ideal for fastening dissimilar materials like metal to wood or plastic without needing additional hardware, making them a go-to solution for many projects.
- Maintenance and Repair: Their design allows for repeated assembly and disassembly, which is perfect for products requiring regular maintenance, such as HVAC systems or modular furniture.
- Thin or Brittle Materials: When working with thin or brittle materials, self-tapping screws provide a reliable fastening method where traditional methods may fail.
Do You Pre-Drill for Self-Tapping Screws?
Pre-drilling can be beneficial but isn’t always necessary. For harder materials, like metal, drilling a pilot hole helps ensure proper thread engagement and prevents damage. When working with thicker materials, pre-drilling facilitates easier installation and reduces the force needed to create threads. However, for softer materials like wood and plastic, sharp-tipped self-tapping screws can create their own holes without the need for pre-drilling, although a pilot hole can still help guide the screw and prevent misalignment.
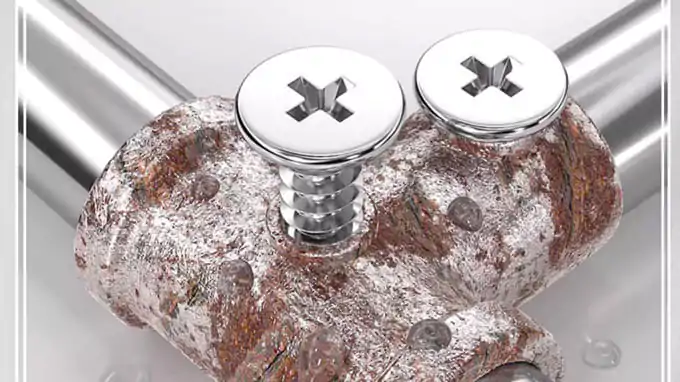
How to Use Self-Tapping Screws?
Using self-tapping screws is straightforward if you follow these steps:
- Choose the Right Screw: Select the appropriate type based on the material and thickness.
- Pre-Drill Pilot Holes (if needed): For hard materials, drill a hole slightly smaller than the screw diameter. For soft materials, this step can be skipped.
- Insert and Tighten the Screw: Align the screw with the marked position, and begin driving it in with a screwdriver or drill at low to medium speed, applying even pressure.
- Check Alignment: Before fully tightening, ensure the materials are correctly aligned. Avoid over-tightening to prevent thread damage.
Conclusion
Self-tapping screws are a great choice for many fastening jobs. They can make their own threads and hold materials together quickly, which makes them very useful in different industries. Whether you’re working with wood, metal, or plastic, knowing the different types and how to use self-tapping screws correctly will help you pick the right one for your project. This ensures everything is held together securely and stays in place.
For more information about our custom self-tapping screws, feel free to contact us or visit our website to learn more.