I often get asked about the differences between ASTM F3125 A325 and A449 bolts. It’s a common point of confusion, but don’t worry—I’m here to clear things up for you. Whether you’re dealing with large-scale projects or just want to ensure you’re using the right bolts, understanding the distinction between these two types is essential.
A325 bolts are lower in strength but can be galvanized for corrosion resistance, making them ideal for structural connections. A449 bolts are similar in strength but cover larger sizes and are more versatile for non-structural uses.
So, let’s dive into the specifics and see which bolt is the right fit for your next project.
1. A325 Bolt: Material, Strength, Coating, and Application
A325 bolts are made from medium carbon steel. They’re specifically designed for structural applications such as bridges and buildings. The strength of A325 bolts is impressive—120,000 psi minimum tensile strength and a yield strength of about 92,000 psi. This makes them a go-to choice for critical structural connections.
The great thing about A325 bolts is that they can be galvanized, making them resistant to corrosion. If you’re working on a project in a humid or outdoor environment, like a bridge or a highway, galvanized A325 bolts are your best bet. The extra layer of protection makes these bolts last longer, even in tough weather conditions.
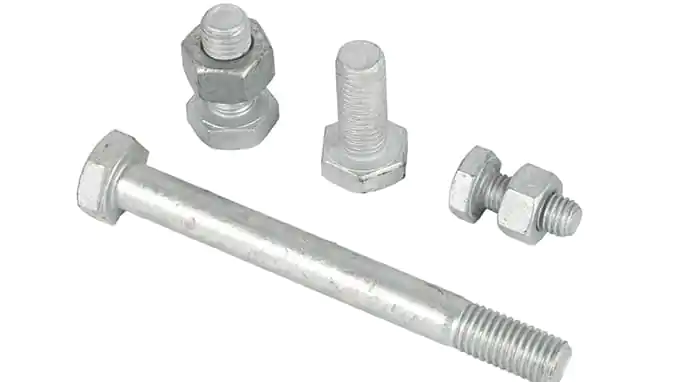
Another feature that sets A325 bolts apart is the design of their threads. The threaded section is kept out of the shear plane, which helps in maintaining the joint’s strength, ensuring a more stable and durable connection. It’s these design details that make A325 bolts a popular choice for heavy construction projects where safety and durability are critical.
In summary, if you need a bolt for high-strength structural applications and you’re concerned about corrosion, A325 bolts are a perfect fit. They’re strong, reliable, and can handle tough conditions.
2. A449 Bolt: Material, Strength, Coating, and Application
ASTM A490 bolts are made from high-strength alloy steel, designed for applications requiring superior strength. With a minimum tensile strength of 150,000 psi and yield strength of about 130,000 psi, they are ideal for heavy-duty structural connections like bridges, wind towers, and military equipment.
Unlike A325 bolts, A490 bolts cannot be hot-dip galvanized due to the risk of hydrogen embrittlement. Instead, they can be coated with corrosion-resistant materials like Dacromet, which ensures durability in harsh environments. The shorter thread length in their design keeps threads out of the shear plane, which enhances joint integrity in high-stress applications.
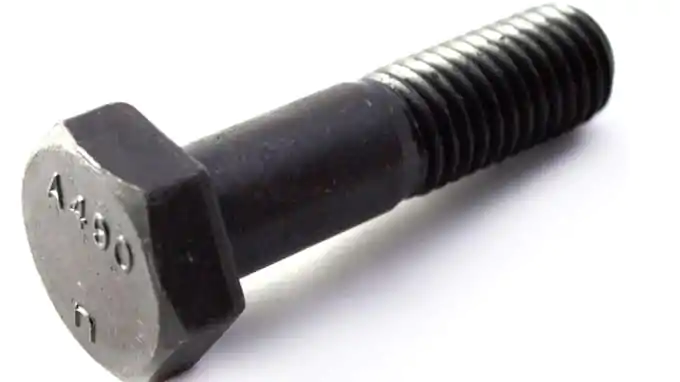
In summary, ASTM A490 bolts are crucial for demanding structural engineering projects where high tensile strength and corrosion resistance are required. Their robust design makes them reliable for critical connections.
3. Comparing ASTM A325 and A449 Bolts
Feature | ASTM A325 | ASTM A449 |
---|---|---|
Material | Medium carbon steel | Steel (more flexible sizes) |
Minimum Tensile Strength | 120 ksi | 150–173 ksi |
Yield Strength | ~92 ksi | ~130 ksi |
Applications | Structural connections | Heavy machinery, large construction |
Coating Options | Can be hot-dip galvanized | Cannot be galvanized |
Diameter Range | Limited | Covers larger diameters |
Key Takeaway: A325 bolts are your best choice for structural projects that need corrosion resistance, while A449 bolts offer more flexibility in size and are perfect for non-structural applications.
4. How to Choose Between ASTM A325 and A449 Bolts?
So, how do you choose between the two? Here are a few things to consider:
Strength Requirements
If your project requires a high-strength bolt for critical structural applications, then A325 bolts are the way to go. With a minimum tensile strength of 120,000 psi, these bolts provide reliable strength for bridges, buildings, and other infrastructure projects.
However, if you’re working on a non-structural application, or you need larger bolts, then A449 is a better option. These bolts have the same tensile strength as A325 but are available in larger diameters, making them suitable for industrial machinery and other general applications.
Corrosion Resistance
For outdoor projects or those exposed to harsh conditions, A325 bolts can be galvanized to provide excellent corrosion resistance. This makes them ideal for highways, bridges, and other outdoor structures that need protection from rust.
A449 bolts, on the other hand, don’t require galvanization. However, they can still be coated with materials like zinc plating or Dacromet, which offers some level of protection without the need for galvanization. This makes A449 a good choice for projects that don’t require as much corrosion resistance.
Application Context
In most cases, if you’re dealing with structural applications, A325 bolts are the go-to solution. But if your project is more about general machinery or you need larger-sized bolts, then A449 is the right choice.
Conclusion
In summary, both A325 and A449 bolts have their strengths, but they serve different purposes. If you’re working on structural projects where corrosion resistance is important, A325 bolts are your best option. For non-structural projects where larger bolt sizes and more versatility are needed, A449 bolts will serve you well.
Remember, always consider the specific requirements of your project when choosing between these two types of bolts. And if you ever need more guidance, feel free to reach out—I’m happy to help!
For more information on fasteners or if you need help selecting the right bolt for your project, contact us at Shanghai Hengrui Industry Co., Ltd or email me at info@hrfastener.com.