When working with fasteners, it’s easy to overlook the importance of material compatibility. Choosing the right fasteners for aluminum can make or break the durability of your project. In this post, I’ll address a common question: Can you use stainless steel screws in aluminum? Let’s dive in.
Yes, stainless steel is the preferred choice for fasteners when securing aluminum materials. However, be mindful of galvanic corrosion. To prevent this, use insulating washers or coatings, and make sure the aluminum’s surface area is larger than the stainless steel screws to reduce corrosion risk.
Now that we’ve covered stainless steel and aluminum, let’s take a closer look at the interaction between stainless steel and galvanized steel, and how to prevent corrosion in this combination. For more details, check out our guide on stainless steel and aluminum used together.
Key Considerations for Using Stainless Steel Screws in Aluminum
When using stainless steel screws in aluminum, several factors can impact the long-term success of your project. Here’s what you need to watch out for:
1. Galvanic Corrosion
This is the main issue. Galvanic corrosion happens when two dissimilar metals come into contact with each other in the presence of moisture or an electrolyte (think salty air, water, or other corrosive environments). Stainless steel and aluminum are both metals with different electrochemical properties. When paired together, one metal will corrode faster than the other.
The aluminum tends to act as the anode (the more reactive metal), while stainless steel acts as the cathode. This means the aluminum is at risk of degrading much faster than it normally would. It’s particularly concerning in environments that are damp or exposed to saltwater, where this reaction is accelerated.
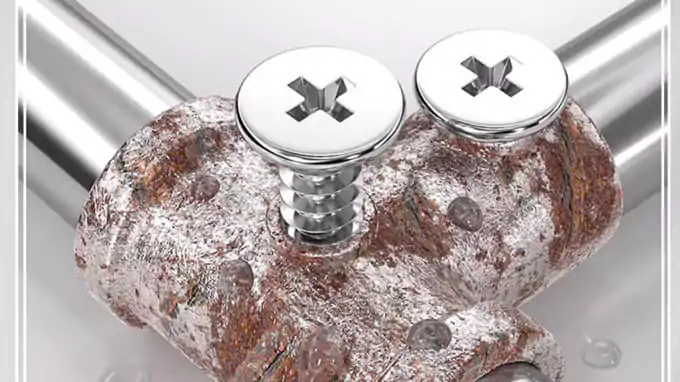
2. Surface Area Matters
The next consideration is the surface area of the aluminum. The larger the aluminum surface area compared to the stainless steel screw, the better it can withstand galvanic corrosion. This is because the aluminum, as the anode, will corrode at a higher rate when the surface area is small.
The idea is to ensure that the aluminum has enough mass to avoid being eaten away by the corrosion process. So, if you’re designing or selecting materials for a project, try to balance the surface areas as best you can.
3. Isolation Techniques
One of the best ways to prevent galvanic corrosion is by isolating the metals. There are several ways to do this:
- Insulating Washers: You can use plastic or rubber washers to physically separate the stainless steel screws from the aluminum surface. This creates a barrier that prevents direct contact, reducing the chances of galvanic corrosion.
- Coatings: Another effective way to reduce the risk of galvanic corrosion is to apply a protective coating or paint to both metals. A non-reactive coating can act as an electrical insulator, reducing the risk of corrosion.
- Anodizing Aluminum: Anodizing is a process that treats aluminum to create a thick oxide layer. This layer enhances corrosion resistance and makes it harder for the metals to interact. It’s especially useful in harsh environments.
Now that you know the key considerations, let’s look at the best methods to prevent galvanic corrosion when using stainless steel screws in aluminum.
Best Methods to Prevent Galvanic Corrosion with Stainless Steel Screws in Aluminum
As a fastener specialist, I’ve learned a few tricks to help you avoid the headaches caused by galvanic corrosion. Here’s how you can prevent it from ruining your project:
1. Use Insulating Barriers
The first step in avoiding galvanic corrosion is to use insulating materials. This includes:
- Plastic or Rubber Washers: These simple materials are a game-changer. By placing them between the stainless steel screws and aluminum, you create a physical barrier that stops the two metals from touching. It’s a quick and easy solution that works wonders.
- Gaskets: Similar to washers, gaskets made from insulating materials can also serve as a protective barrier.
2. Apply Protective Coatings
Protective coatings are another highly effective method to prevent galvanic corrosion. Coatings like epoxy primers can create a barrier that reduces the risk of electrochemical reactions. For aluminum, anodizing it is a great option. It adds an extra layer of protection and strengthens the metal’s resistance to corrosion.
3. Ensure Proper Surface Area
As mentioned earlier, the aluminum surface area should be significantly larger than the stainless steel screws. This helps minimize the galvanic reaction. The more surface area your aluminum part has, the less likely it is to corrode.
4. Avoid Moisture Exposure
Water is an electrolyte that can speed up galvanic corrosion, so it’s important to keep the assembly as dry as possible. In harsh environments like marine settings or humid climates, you need to take extra precautions to minimize exposure to water or salty air.
5. Use Corrosion Inhibitors
Another trick to help prevent corrosion is to apply lubricants or anti-corrosion pastes to the threads and contact points of the fasteners. These products reduce friction and help protect the metal from moisture.
6. Regular Maintenance
Lastly, don’t forget about maintenance. Regularly inspect your aluminum and stainless steel components to catch any signs of corrosion early. Reapply protective coatings as necessary and clean the surfaces to prevent moisture from accumulating.
What Happens When Stainless Steel and Galvanized Steel Are Combined?
You may also wonder if there’s a galvanic reaction between stainless steel and galvanized steel. The short answer is: yes, there is.
Galvanized steel has a coating of zinc, which, when in contact with stainless steel, can create a galvanic reaction in the presence of moisture. Galvanized steel, due to its zinc coating, tends to corrode faster than stainless steel in this pairing. Zinc (on the galvanized steel) is a more reactive metal than stainless steel, which ranks higher on the galvanic series. When these metals are coupled together, the zinc will corrode faster than it would if it were alone. Like aluminum, galvanized steel will act as the anode, corroding more quickly in moist or saline environments, while stainless steel will act as the cathode.
If you’re using stainless steel screws with galvanized steel, you’ll want to apply the same principles to prevent galvanic corrosion. Insulating washers, protective coatings, and regular maintenance are your best defense.
Preventing Corrosion Between Galvanized and Stainless Steel
To prevent galvanic corrosion between galvanized steel and stainless steel, here are a few strategies:
- Electrical Isolation: Use plastic or rubber washers to isolate the two metals.
- Protective Coatings: Apply paint or other coatings to reduce moisture exposure.
- Design Considerations: Ensure that the stainless steel surface area is larger than the galvanized surface.
- Regular Maintenance: Inspect regularly for signs of corrosion and clean the surfaces as needed.
Conclusion
In conclusion, while using stainless steel screws in aluminum is perfectly fine, there are a few precautions you must take to prevent galvanic corrosion. By using insulating barriers, applying coatings, and maintaining the assembly, you can ensure a long-lasting, corrosion-free connection.
Remember, prevention is key. With the right precautions, you can confidently use stainless steel screws in aluminum without worrying about corrosion eating away your project.
If you’re looking for top-quality fasteners for your project, don’t hesitate to reach out to us at Hengrui. We offer a wide range of fasteners, including custom-made options, that can meet your specific needs.