Stainless steel fasteners are widely used across industries for their durability and corrosion resistance. However, when selecting fasteners for engineering or industrial use, mechanical strength becomes a critical factor. This article provides a detailed analysis of the tensile strength, material grades, and application considerations of stainless steel fasteners—particularly for procurement professionals, engineers, and B2B technical decision-makers.
Most stainless steel fasteners conform to ISO 3506 Class 70, which specifies a minimum tensile strength of 700 MPa. Unmarked fasteners are typically considered Class 50 with a minimum tensile strength of 500 MPa. Although generally not as strong as hardened carbon steel fasteners, stainless steel fasteners offer superior corrosion resistance and are ideal for environments with high exposure to moisture, chemicals, or salt.
Why Does Fastener Strength Matter in Industrial Design?
In industrial and infrastructure applications, fastener failure can result in operational downtime, safety risks, and significant maintenance costs. For example, structural engineers require fasteners with reliable tensile performance under static and dynamic loads. Equipment manufacturers demand components with sufficient fatigue strength to withstand vibration and repeated stress cycles. In energy sectors such as wind or solar, long-term outdoor durability and structural stability are essential.
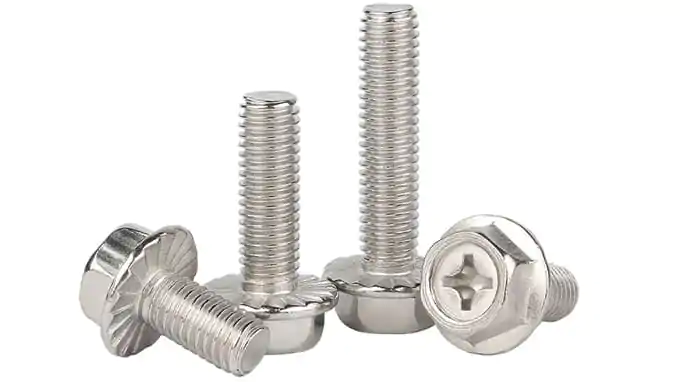
What Is the Tensile and Yield Strength of Stainless Steel Fasteners?
Stainless steel fasteners made from 304 or 316 grade typically exhibit a yield strength of approximately 207 MPa and an ultimate tensile strength around 483 MPa in annealed condition. While this is lower than high-grade carbon steel fasteners (e.g., Grade 8 with tensile strength >1,200 MPa), it is adequate for most medium-load industrial applications. The selection of appropriate fastener class—such as ISO 3506 Class 70—is crucial to ensure performance and compliance with structural load requirements.
What Are the Differences Between Stainless Steel Grades?
Among stainless steel fastener grades, 304 and 316 are the most commonly used. Grade 316 contains molybdenum, enhancing both strength and corrosion resistance, particularly in chloride-rich or marine environments. For applications requiring higher mechanical strength, 410 stainless steel offers increased hardness due to its higher carbon content, although with a trade-off in corrosion resistance. Understanding the mechanical trade-offs between grades is essential for safe and efficient design.
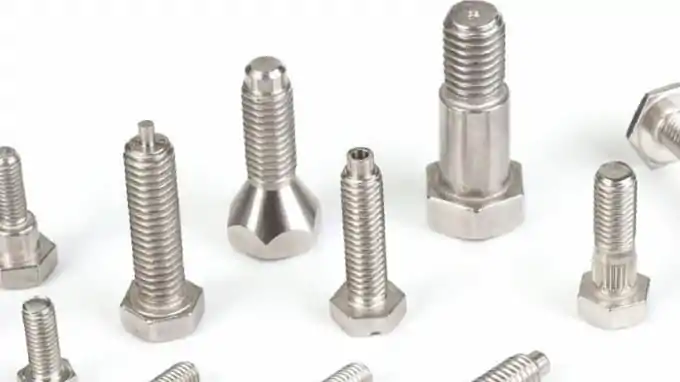
How Do Stainless Steel Fasteners Compare to Carbon Steel?
While stainless steel fasteners offer reliable corrosion resistance, their mechanical strength is generally lower than that of carbon steel fasteners. Grade 5 carbon steel fasteners have tensile strengths around 830 MPa, while Grade 8 can exceed 1,200 MPa. This makes carbon steel preferable for high-load-bearing or structural applications. However, these fasteners require protective coatings to prevent corrosion, making stainless steel a more suitable choice in corrosive or exposed environments.
Are Stainless Steel Fasteners Prone to Breakage?
It is a misconception that stainless steel fasteners are prone to easy breakage. When used within their design load range, they provide dependable mechanical performance. Failures usually occur due to improper torque application, galling, or mismatch between bolt grade and load requirements. In applications involving high vibration or thermal expansion, selecting the correct thread design and applying anti-galling lubricants are critical to ensuring performance.
Where Are Stainless Steel Fasteners Commonly Used?
For structural construction, stainless steel fasteners are often specified in curtain wall systems, pedestrian bridges, and steel framework connections due to their long-term environmental resistance. In the machinery sector, 410-grade fasteners are preferred for parts under wear or mechanical stress. In the automotive industry, stainless fasteners are commonly used in battery mounts and EV structural components for their non-reactive properties and corrosion protection.
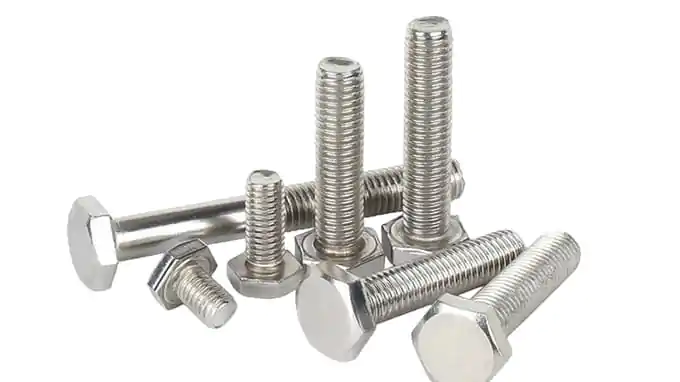
In energy infrastructure, particularly wind turbines and photovoltaic support systems, fasteners must resist corrosion over decades. Grade 316 fasteners meet this requirement, offering resistance to acidic rain, UV exposure, and salt spray. For oil and gas pipelines or offshore platforms, fasteners must not only offer mechanical strength but also resist sulfide stress cracking and chloride corrosion.
What Are the Strength and Performance Specifications of Stainless vs Carbon Steel Fasteners?
Property | Class 70 Stainless Steel | Grade 5 Carbon Steel | Grade 8 Carbon Steel |
---|---|---|---|
Min. Tensile Strength | 700 MPa | 830 MPa | 1,200 MPa |
Yield Strength | ~207 MPa | ~660 MPa | ~1,030 MPa |
Corrosion Resistance | Excellent | Low (plated) | Low (plated) |
Cost | Higher | Lower | Moderate |
Best Use | Outdoor, corrosion-prone settings | High-load indoor applications | Structural, load-bearing assemblies |
How Should Engineers and Buyers Choose the Right Stainless Fastener?
Stainless steel fasteners combine corrosion resistance with medium mechanical strength, making them ideal for applications where environmental exposure is a concern but ultra-high load is not the primary factor. Engineers and procurement professionals should select fastener types based on standardized strength classes, environmental exposure, and expected mechanical stress. Adhering to ISO 3506 classifications ensures consistent performance and safety.
For high-performance and critical applications, careful matching of grade, class, and installation method is essential. When in doubt, refer to tensile and shear strength tables or consult with fastener manufacturers to ensure compliance with engineering specifications.
For more information on how Hengrui can meet your fastener and machining part needs, feel free to Contact Us at info@hrfastener.com or visit our website Hengrui Fastener.