Industrial fasteners are important tools used in a variety of industries. Whether in automotive manufacturing, aerospace, or construction, they serve to secure components together, ensuring that assemblies are structurally sound. Essential in modern engineering, fasteners are critical connections in systems and structures where strength and reliability are paramount. In this article, we will define, detail the types and examine applications for industrial fasteners, providing perspective on the role these tools play in a variety of industries.
An industrial fastener is a device that connects two or more components, forming a mechanical joint. These fasteners can create non-permanent connections (like bolts and screws) or permanent ones (like welds and rivets) depending on the application requirements. They are crucial for maintaining the structural integrity of assemblies by holding parts together under various loads and conditions. These fasteners are widely used across industries such as construction, automotive, aerospace, machinery, and even electronics.
Fasteners are designed to withstand significant forces and can resist tension, shear, and compression that might otherwise cause assembly failure. Depending on the design and materials, they can provide strength, flexibility, or resistance to a variety of environmental factors, including corrosion, heat, and moisture.
What Are the Common Types of Industrial Fasteners?
Industrial fasteners come in various shapes and sizes, each serving specific purposes. Below are some of the most common types:

- Bolts: Cylindrical fasteners with a head at one end and threads for securing with a nut. Bolts are often used in applications where disassembly is needed, such as in machinery or construction. They are available in many different sizes, materials, and grades to suit specific applications.
- Nuts: Hexagonal or other shaped fasteners that fit onto bolts to secure them. Nuts play a critical role in locking the bolt in place, ensuring that the connection remains firm and secure under various stresses.
- Screws: Fasteners that are driven into materials to hold them together, often without needing a nut. Screws are more versatile than bolts, as they can be used in a wide range of materials, including wood, metal, and plastic. They can also offer higher holding power due to their threaded nature.
- Washers: Used with bolts and nuts to distribute loads and prevent damage to surfaces. Washers also provide additional friction, which helps in preventing loosening from vibrations, making them essential in automotive, industrial, and construction applications.
- Rivets: Permanent fasteners that join materials by deforming the tail end after insertion. Rivets are especially useful in applications where welding is not feasible, and they create a permanent, secure bond. Common in the aerospace industry, rivets are used to join parts of aircraft bodies or metal components that cannot be easily disassembled.
How Do Industrial Fasteners Work?
An industrial fastener is a mechanical device that connects two or more parts to form a joint. It resists forces like tension, shear, or compression, which otherwise would cause parts to separate or move out of alignment. By holding parts together, fasteners maintain the structural integrity of an assembly, whether temporary or permanent.
- Temporary fasteners, such as bolts and screws, allow for disassembly, which is useful for repairs or maintenance.
- Permanent fasteners, such as rivets and welds, are designed to create an irreversible bond between materials, providing a high level of security and stability.
What Materials Are Industrial Fasteners Made Of?
Most industrial fasteners are made of steel, stainless steel, aluminum, copper, and plastics, depending on the specific needs for strength, corrosion resistance, and weight.
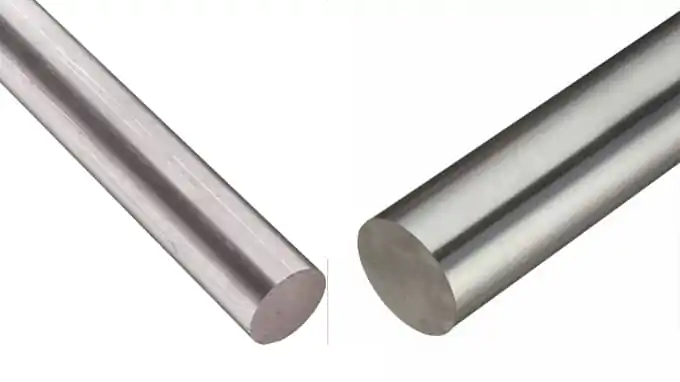
- Steel is widely used for its strength and cost-effectiveness, making it ideal for heavy-duty applications in construction and automotive industries.
- Stainless steel is known for its corrosion resistance, which makes it ideal for use in environments exposed to moisture or chemicals, such as in marine, food processing, and medical equipment.
- Aluminum fasteners are lightweight and resistant to corrosion, making them ideal for aerospace and automotive applications.
- Copper-based alloys are commonly used in applications requiring electrical conductivity, such as in electronics.
- Plastics are used for lightweight applications where corrosion resistance and electrical insulation are required.
What Are Industrial Fasteners Used For?
Industrial fasteners are used to connect two or more components to form a mechanical joint that can either be temporary or permanent. They are essential in applications where parts must remain securely fastened under various conditions and forces, such as tension, shear, or compression. These fasteners maintain the stability and functionality of the assembled components even when placed under heavy loads and stress.
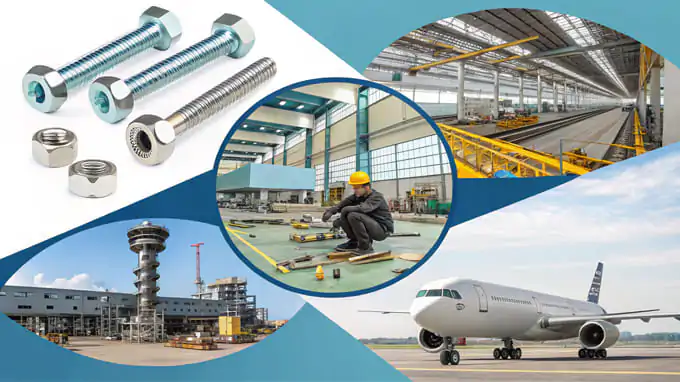
They are commonly used in:
- Machinery: Fasteners hold moving parts of machines in place, allowing for smooth operation while preventing failure.
- Vehicles: In automobiles, trucks, and motorcycles, fasteners are essential in securing critical components, such as engines, chassis, and body panels.
- Electronics: Small fasteners, such as screws and rivets, are often used to hold components in place within devices like smartphones, computers, and household appliances.
What Types of Fasteners Are Used in Construction?
In construction, fasteners such as bolts, nuts, washers, screws, and rivets are vital to assure the safety and longevity of buildings and infrastructure. These fasteners are used to fasten structural components such as beams, girders, and walls to ensure that they stay in place under different load conditions, including tension and compression. The strength and reliability of these fasteners are critical to the overall stability of the structure.
- Bolts and nuts are widely used in steel-frame buildings, bridges, and other large structures.
- Screws are often used in wood-frame construction, holding panels, beams, and drywall in place.
- Rivets were historically used in the construction of bridges and steel-frame buildings but are still used in specialized applications where welding or bolts are not feasible.
Conclusion
Industrial fasteners are instrumental in ensuring the integrity and reliability of a wide range of structures and machinery. Whether in construction, automotive or aerospace applications, these fasteners guarantee that parts remain securely connected and perform optimally under diverse conditions. Industrial fasteners are essential in modern engineering, without which the assembly of machinery, vehicles and infrastructure would be impossible. Their versatility in materials and uses ensures that they continue to play a crucial role in the formation of safe, reliable and durable systems across the globe.
For more information on fasteners or if you need help selecting the right bolt for your project, contact us at Shanghai Hengrui Industry Co., Ltd or email me at info@hrfastener.com.