Specialty fasteners are critical components used to join or secure two or more parts together in industries that demand high strength, precision, and durability. Unlike regular fasteners, which are often used in general applications, specialty fasteners are designed for specific tasks where ordinary fasteners may not be reliable or efficient. These fasteners are often custom-made to meet precise requirements and are essential in fields like aerospace, automotive, construction, and marine engineering.
In this article, we’ll dive deeper into what specialty fasteners are, common examples, the materials used to make them, and why they’re crucial in certain industries.
Specialty fasteners are made from high-performance materials such as steel alloys or titanium, and they come in different forms, including screws, bolts, nuts, washers, and studs. They are designed to withstand extreme conditions, including high pressures, high temperatures, and corrosive environments. This makes them essential in industries that rely on safety and long-term reliability, such as aerospace, military, and heavy machinery.
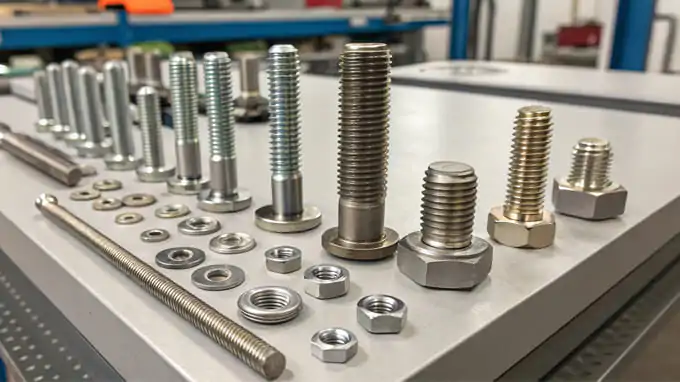
What Are Specialty Fasteners?
Specialty fasteners differ from regular fasteners in that they are designed for specific applications where standard fasteners might fail. These fasteners are customized to meet the needs of different industries that require strength, durability, and precision. They are often made from materials that resist corrosion, wear, and high temperatures. For example, in the aerospace industry, fasteners need to be light but extremely strong to withstand high altitudes and extreme temperature changes. In construction, fasteners must be able to hold massive loads while being resistant to environmental factors like rust and corrosion.
The role of specialty fasteners is to ensure that critical components stay securely fastened, even in challenging and demanding environments. These fasteners are used in a wide range of industries, including automotive, energy, marine, aerospace, and military sectors.
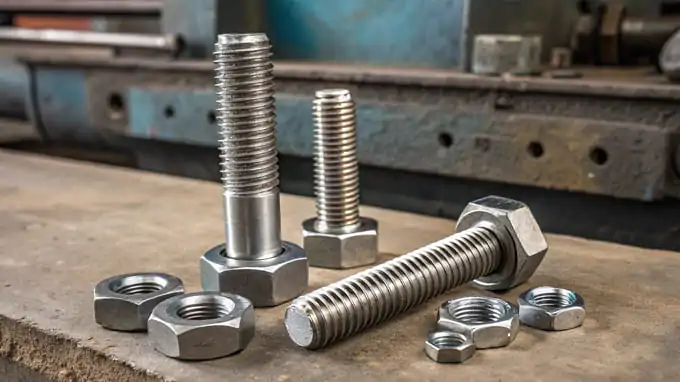
Common Examples of Specialty Fasteners
There are several types of specialty fasteners, each designed to meet the unique needs of different industries. Here are a few common types:
- Socket Head Screws: These are used when you need high torque (twisting force) and precision. They are commonly found in machinery, automotive parts, and mechanical equipment.
- High-Tensile Bolts: These bolts are designed to withstand extremely high levels of stress and pressure. They are used in construction, mining, and heavy machinery to keep structures secure and functional.
- Stainless Steel Screws: Stainless steel is highly resistant to rust and corrosion, making it the material of choice for industries like marine engineering, chemical processing, and food production.
- Titanium Fasteners: Titanium is a lightweight yet extremely strong material that performs well at high temperatures. It is widely used in the aerospace industry, as well as in high-performance automotive applications, where strength and lightness are critical.
- Weld Studs: These fasteners are used in welding applications, where metal parts need to be joined by heat. Weld studs are commonly used in the construction and manufacturing industries for projects requiring long-term durability.
Each of these fasteners is designed to perform specific tasks that ordinary fasteners cannot. The choice of fastener type depends on the demands of the industry and the application.
Materials for Specialty Fasteners
The material used to make a fastener is crucial to its performance. The right material ensures that the fastener can endure the stress, temperature, and environmental factors that it will face in its application. Let’s take a closer look at some of the most common materials used for specialty fasteners:
- Carbon Steel:
Carbon steel is strong and inexpensive, making it ideal for applications in heavy machinery, construction, and automotive industries. However, carbon steel is prone to rust and corrosion when exposed to moisture, which is why it may not be suitable for all environments. - Stainless Steel:
Stainless steel is known for its resistance to rust and corrosion, making it perfect for use in harsh environments like the marine, chemical, and food processing industries. Its ability to resist wear and tear also makes it ideal for high-stress applications like oil rigs and chemical plants. - Titanium:
Titanium is one of the lightest yet strongest metals available. It performs exceptionally well in aerospace and high-performance automotive applications. Titanium fasteners can withstand high temperatures and are resistant to corrosion in both saltwater and high-heat environments, making them a preferred choice for critical operations. - Alloy Steel:
Alloy steel is a mixture of steel and other elements, designed to increase its strength and resistance to wear. It’s commonly used in construction, energy sectors, and mining, where high tensile strength and durability are required to withstand extreme conditions like high pressure and temperature. - Brass and Bronze:
These materials are often chosen for their corrosion resistance and electrical conductivity. They are widely used in electrical and marine engineering applications. Bronze, for example, is often used in marine environments due to its ability to resist corrosion from saltwater.
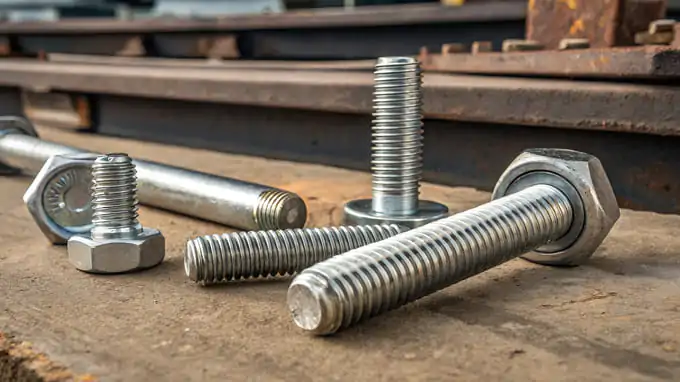
Why Use Specialty Fasteners?
Specialty fasteners offer several key advantages that make them invaluable in industries where reliability and performance are essential:
- Customization:
Specialty fasteners can be custom-designed to meet specific requirements for size, shape, material, and strength. This is particularly important in industries like aerospace and military, where the fastener must meet exact specifications to ensure safety and functionality. - Durability:
Unlike regular fasteners, specialty fasteners are made from high-performance materials that can withstand harsh conditions. Whether it’s high pressure, extreme temperatures, or exposure to corrosive environments, specialty fasteners are built to last longer and perform better under stress. - Reliability:
In industries where failure is not an option, such as defense, aerospace, and nuclear energy, the use of specialty fasteners ensures that equipment remains secure and functional. These fasteners are designed to handle the most demanding environments, reducing the risk of accidents or failures. - Corrosion Resistance:
Specialty fasteners made from materials like stainless steel or titanium are resistant to rust and corrosion. This makes them ideal for use in marine, chemical, and oil & gas industries, where exposure to harsh environments is common. - Cost-Effectiveness:
While specialty fasteners may cost more upfront, their long lifespan and ability to reduce maintenance costs can result in long-term savings. Industries that rely on machinery and infrastructure need fasteners that won’t fail easily, and investing in quality specialty fasteners can ultimately save on repair and replacement costs.
What Are the Toughest Fasteners?
The toughest fasteners are those designed to handle the highest stress and toughest conditions. For example:
- Wedge Anchors: These fasteners are commonly used in construction and heavy machinery applications to secure objects to concrete and masonry. They work by expanding inside the material to create a firm hold, ensuring that the fastener stays in place under extreme conditions.
- High-Tensile Bolts: These bolts are made from alloy steel and are built to handle significant stress and pressure. They are commonly used in industries like oil & gas, energy, and mining, where heavy loads and high-pressure environments are the norm.
- Stud Bolts: Often used in oil refineries, power plants, and nuclear reactors, stud bolts are designed to handle high-temperature and high-pressure applications, making them among the toughest fasteners available.
Conclusion
In industries where performance, reliability, and durability are essential, specialty fasteners are crucial. They are used in sectors like aerospace, automotive, construction, and energy, where standard fasteners simply won’t do. Whether they are made from stainless steel, titanium, or alloy steel, these fasteners are built to meet the demanding needs of critical applications.
By choosing the right specialty fastener, industries can ensure long-term performance, safety, and cost-effectiveness. If you’re working on a project that requires precision and durability, make sure you choose the right specialty fastener for the job.