Titanium fasteners are widely used in industries that demand high strength, corrosion resistance, and lightweight materials. These industries include aerospace, automotive, marine, medical, and chemical processing. Unlike steel fasteners, titanium fasteners offer an exceptional strength-to-weight ratio, meaning they provide excellent mechanical properties while remaining lightweight.
Among the various grades of titanium fasteners, Gr2[^1], Gr5[^2], and Gr7[^3] are the most commonly used. Each of these grades has distinct properties, making them suitable for specific applications. Gr2 is known for its excellent corrosion resistance, Gr5 for its high strength, and Gr7 for its superior resistance in extreme chemical environments. Understanding their differences will help you determine the best choice for your project.
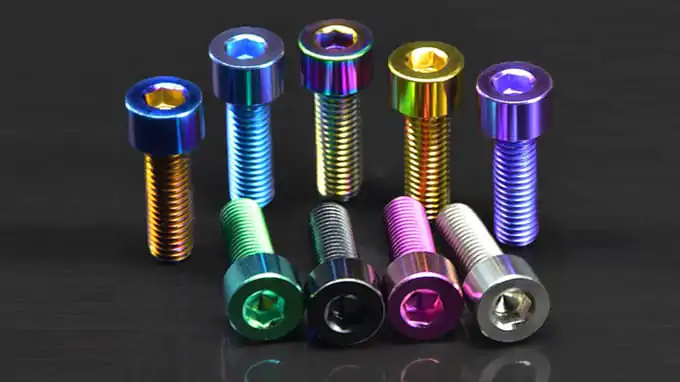
What Are Titanium Gr2, Gr5, and Gr7 Fasteners?
Titanium Gr2, Gr5, and Gr7 fasteners are bolts, screws, nuts, and washers made from titanium alloys designed for various industrial applications. These fasteners are highly durable and resistant to harsh conditions, making them a preferred choice for engineers and manufacturers in demanding industries.
Each grade offers unique benefits. Gr2 fasteners are best for corrosion-resistant applications, Gr5 fasteners are used in high-stress environments requiring superior strength, and Gr7 fasteners are ideal for extreme chemical conditions. Selecting the appropriate grade depends on factors such as mechanical strength, resistance to environmental conditions, and cost considerations.
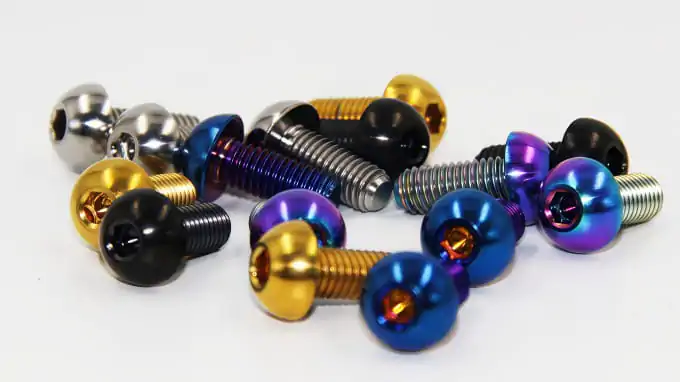
What Is Gr2 Titanium?
Titanium Grade 2 (Gr2) is a commercially pure titanium alloy that contains at least 99.2% titanium, with small amounts of iron, oxygen, nitrogen, and other elements. It is one of the most commonly used titanium grades due to its balance of strength, corrosion resistance, and affordability.
One of the key advantages of Gr2 titanium fasteners is their exceptional resistance to corrosion, particularly in saltwater, chlorine, and mildly acidic environments. This makes them an excellent choice for marine applications, desalination plants, and chemical processing facilities. Additionally, Gr2 fasteners are lightweight and easy to form and weld, making them ideal for projects requiring flexible and corrosion-resistant components.
In terms of mechanical properties, Gr2 fasteners have a tensile strength of approximately 344 MPa and a yield strength of 275 MPa. While not as strong as Gr5 fasteners, they are highly durable and offer long-term reliability in applications where corrosion resistance is more critical than extreme strength.
What Is Gr5 Titanium?
Titanium Grade 5 (Gr5), also known as Ti-6Al-4V, is an alloy containing 6% aluminum and 4% vanadium, making it significantly stronger than commercially pure titanium. This alloy is one of the most widely used titanium grades in high-performance industries due to its exceptional strength, durability, and resistance to high temperatures.
The high strength-to-weight ratio of Gr5 titanium fasteners makes them particularly useful in the aerospace and automotive industries. Aircraft manufacturers use Gr5 fasteners in structural components, landing gear, and engine parts, where reducing weight without compromising strength is essential. Similarly, high-performance sports cars and motorcycles incorporate Gr5 fasteners to enhance performance while minimizing weight.
With a tensile strength of approximately 1000 MPa and a yield strength of 950 MPa, Gr5 titanium is more than three times stronger than Gr2. It also has excellent fatigue resistance, allowing it to withstand repeated stress without failure. However, Gr5 fasteners are slightly less corrosion-resistant than Gr2, which should be considered when selecting materials for applications in highly corrosive environments.
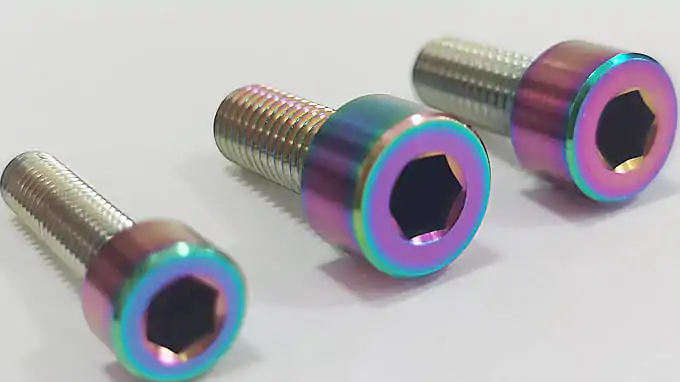
What Is Gr7 Titanium?
Titanium Grade 7 (Gr7) is similar to Gr2 but contains a small percentage of palladium (0.12-0.25%), which significantly enhances its resistance to corrosion in aggressive environments. This makes Gr7 one of the most corrosion-resistant titanium alloys available, making it ideal for highly acidic and high-temperature applications.
One of the main advantages of Gr7 titanium fasteners is their ability to withstand extreme chemical exposure, such as in chloride-heavy and oxidizing environments. This makes them a preferred choice for chemical processing plants, power generation facilities, and offshore oil and gas applications. Additionally, Gr7 exhibits excellent resistance to crevice corrosion, which is a common issue in fasteners exposed to seawater and harsh chemicals.
Despite being similar in strength to Gr2 (with a tensile strength of 345 MPa and a yield strength of 275 MPa), Gr7’s enhanced corrosion resistance makes it significantly more durable in highly aggressive conditions. This added durability comes at a higher cost due to the presence of palladium, making Gr7 one of the most expensive titanium fastener options.
What Is the Difference Between Gr2 and Gr5 Titanium?
Titanium Gr2 and Gr5 fasteners differ primarily in strength, corrosion resistance, workability, and cost. Gr2 is a commercially pure titanium with a tensile strength of 344 MPa, offering excellent corrosion resistance, especially in marine and chemical environments. It is also lightweight and easy to form and weld, making it a preferred choice for applications requiring simple fabrication and long-term durability in corrosive conditions.
In contrast, Gr5 (Ti-6Al-4V) is an alloy containing 6% aluminum and 4% vanadium, which significantly increases its strength (1000 MPa tensile strength) and fatigue resistance. This makes Gr5 ideal for aerospace, automotive, and medical applications, where high performance and durability are required. However, Gr5 is more expensive and slightly harder to machine due to its added alloying elements.
Gr2 is best for corrosion resistance and easy fabrication, while Gr5 is ideal for high-strength applications like aerospace and automotive.
Property | Gr2 Titanium | Gr5 Titanium |
---|---|---|
Strength | Moderate (344 MPa) | High (1000 MPa) |
Corrosion Resistance | Excellent | Very good |
Weight | Lightweight | Slightly heavier |
Workability | Easy to form and weld | More difficult to form |
Cost | Lower | Higher due to alloying elements |
What Is the Difference Between Gr2 and Gr7 Titanium?
While both Gr2 and Gr7 are commercially pure titanium, the key difference is the addition of palladium (0.12-0.25%) in Gr7, which enhances corrosion resistance in extreme environments. Gr2 is already highly resistant to corrosion, making it ideal for marine, aerospace, and chemical processing applications. With moderate strength (344 MPa tensile strength) and excellent weldability, it is widely used in less aggressive environments.
Gr7, however, provides superior resistance to highly acidic and oxidizing conditions, such as those found in chemical processing plants, nuclear power facilities, and offshore structures. Although Gr7 shares similar mechanical properties with Gr2, its enhanced corrosion resistance makes it the preferred choice for environments where Gr2 may not provide long-term durability.
Gr7 is recommended for extreme conditions where corrosion is a major concern, while Gr2 is a cost-effective option for general corrosion resistance.
Property | Gr2 Titanium | Gr7 Titanium |
---|---|---|
Strength | Moderate (344 MPa) | Moderate (345 MPa) |
Corrosion Resistance | Excellent | Superior (due to palladium) |
Best Used In | Marine, aerospace, chemical processing | Extreme chemical environments |
What Is the Difference Between Gr5 and Gr7 Titanium?
Gr5 and Gr7 titanium serve different purposes due to their distinct mechanical and chemical properties. Gr5 (Ti-6Al-4V) is a high-strength titanium alloy with exceptional durability (1000 MPa tensile strength) and good corrosion resistance, making it suitable for aerospace, automotive, and medical applications. It is widely used in high-performance industries where weight reduction and mechanical strength are critical.
On the other hand, Gr7 is primarily chosen for its exceptional corrosion resistance. With similar strength to Gr2 (345 MPa tensile strength), Gr7 is not as strong as Gr5 but is highly resistant to harsh chemical environments, such as acidic and chloride-heavy conditions.
If strength and mechanical performance are your priorities, Gr5 is the better choice. However, if extreme corrosion resistance is required, particularly in acidic or chloride-heavy conditions, Gr7 is the best option.
Property | Gr5 Titanium | Gr7 Titanium |
---|---|---|
Strength | High (1000 MPa) | Moderate (345 MPa) |
Corrosion Resistance | Very good | Exceptional |
Best Used In | Aerospace, automotive, medical | Chemical processing, marine |
Understanding these differences helps engineers and manufacturers select the right fastener for their specific industry needs.
Titanium Gr2, Gr5, and Gr7 Fasteners Comparison Table
Property | Gr2 Titanium | Gr5 Titanium | Gr7 Titanium |
---|---|---|---|
Strength | Moderate (344 MPa) | High (1000 MPa) | Moderate (345 MPa) |
Corrosion Resistance | Excellent | Very good | Exceptional |
Best Applications | Marine, chemical processing | Aerospace, automotive, medical | Chemical plants, marine, offshore |
Cost | Affordable | Moderate | High due to palladium |
Titanium Gr2, Gr5, and Gr7 Fasteners Price
The price of titanium fasteners varies depending on the grade, size, and manufacturing process. Generally:
- Gr2 fasteners are the most affordable due to their simple composition.
- Gr5 fasteners are moderately priced because of the additional aluminum and vanadium alloying elements.
- Gr7 fasteners are the most expensive due to the inclusion of palladium, which enhances corrosion resistance in extreme environments.
When selecting titanium fasteners, cost should be weighed against performance requirements, ensuring you choose the most suitable option for your industry.
Conclusion
Titanium fasteners play a crucial role in industries that demand strength, corrosion resistance, and lightweight materials. Gr2, Gr5, and Gr7 are the most commonly used grades, each offering unique benefits:
- Gr2 is best for applications needing superior corrosion resistance at an affordable cost.
- Gr5 is ideal for high-strength applications in aerospace, automotive, and medical industries.
- Gr7 is the best choice for extreme chemical and offshore environments requiring maximum corrosion resistance.
For expert guidance on choosing the right titanium fasteners, contact us today!