Selecting the right bolts for aluminum is crucial, especially when considering the risks of corrosion. If the wrong fasteners are used, corrosion can compromise the strength and longevity of aluminum parts, especially in high-stress applications. By understanding galvanic corrosion and the best types of bolts to use, you can prevent these issues and ensure the durability of your aluminum structures.
Stainless steel bolt is a preferred choice for fasteners when securing aluminum materials. However, there’s a risk of galvanic corrosion if not used correctly. Stainless steel bolt, such as those made from 304 and 316 grades, are commonly used in aluminum applications. The 316 grade is particularly suited for marine environments due to its superior corrosion resistance. Yet, when paired together, aluminum and stainless steel may lead to galvanic corrosion, which can be minimized with proper precautions.
To mitigate galvanic corrosion and ensure the integrity of aluminum materials, it’s essential to understand why stainless steel is a go-to option and explore alternatives that can work in specific applications.
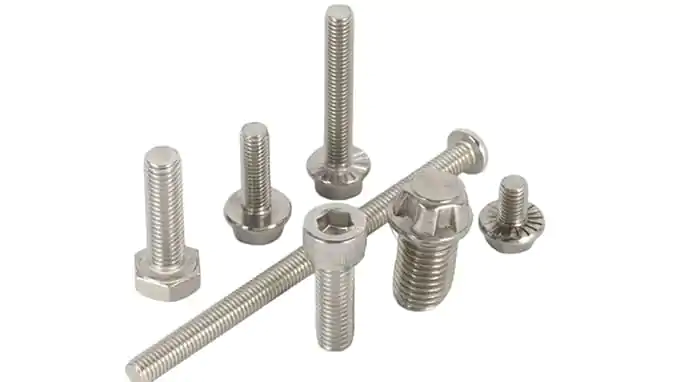
What is Galvanic Corrosion?
Galvanic corrosion occurs when two different metals—such as aluminum and stainless steel—are in electrical contact with each other in the presence of an electrolyte (like water). In this process, the more anodic metal (aluminum) corrodes more quickly than it would alone, while the cathodic metal (stainless steel) remains relatively unharmed. This effect is most problematic when aluminum and stainless steel fasteners are used together without precautions.
However, while galvanic corrosion is a concern, it doesn’t mean you have to avoid using stainless steel fasteners altogether. With the right care and material choices, galvanic corrosion can be mitigated.
Why is Stainless Steel Still the Preferred Choice for Aluminum?
Stainless Steel Bolts:
While stainless steel is resistant to corrosion, it can accelerate galvanic corrosion when in contact with aluminum due to its cathodic nature. Despite this, stainless steel is often the bolt of choice in aluminum applications because of its impressive strength, durability, and resistance to atmospheric corrosion.
- 304 and 316 Stainless Steel: These grades of stainless steel are commonly used for aluminum applications. 316 stainless steel is particularly preferred for cosmetic and harsh environments, such as marine applications, because of its superior resistance to corrosion compared to 304.
The strength and long-lasting durability of stainless steel make it an ideal choice for many applications, even when working with aluminum, as long as proper isolation (like washers or coatings) is used to prevent galvanic corrosion.
What are the Alternatives to Stainless Steel Bolts for Aluminum?
While stainless steel is often the go-to choice, it may not always be the best option for every scenario, especially in environments where corrosion is a higher concern. Here are some alternatives to consider: 5-type-of-fasteners-to-use-with-aluminum-without-corroding
- Aluminum Bolts: These bolts are a natural fit for aluminum parts since they are made from the same material. However, they might not offer the same strength and corrosion resistance as stainless steel, particularly in more demanding environments. Aluminum bolts work well in lightweight applications where corrosion resistance is paramount.
- Titanium Bolts: Titanium bolts are a great alternative for aluminum in high-performance applications, such as aerospace and automotive industries. Titanium is highly resistant to corrosion and is incredibly strong relative to its weight, making it ideal for critical applications. However, titanium bolts are typically more expensive than stainless steel.
- Coated Fasteners: Coatings like zinc plating or anodizing can be applied to steel bolts to reduce the risk of galvanic corrosion when used with aluminum. Zinc plating, for example, provides a sacrificial layer that corrodes before the aluminum, offering an added layer of protection. These bolts can be an excellent choice when you need cost-effective corrosion prevention without sacrificing too much strength.
Can I Use Grade 8 Bolts in Aluminum?
Grade 8 bolts may cause damage to aluminum due to their hardness. The hardness of Grade 8 bolts can cause galling and other issues when paired with aluminum, leading to damage and weakening of the material. For most aluminum applications, it’s better to use bolts that are softer or coated to prevent damage.
Can I Use Galvanized Bolts on Aluminum?
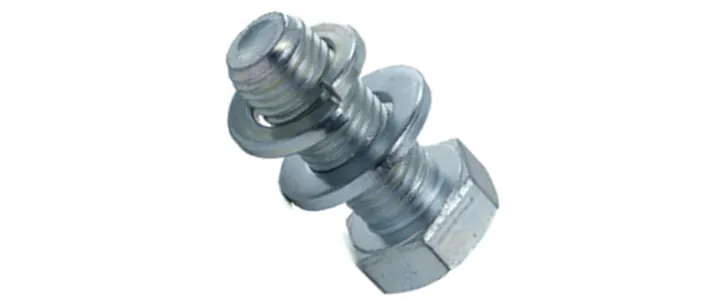
Using galvanized bolts on aluminum is not recommended, as galvanized bolts can cause galvanic corrosion when paired with aluminum. The zinc coating on galvanized bolts can cause the aluminum to corrode faster, especially in moist or salty environments. If you need corrosion protection, consider using stainless steel or coated fasteners instead.
What Fasteners Are Best for Aluminum Boats?
When it comes to aluminum boats, stainless steel fasteners, particularly those made from 316 stainless steel, are often the best choice due to their excellent corrosion resistance, especially in marine environments. Coated fasteners and anodized aluminum bolts are also good alternatives, depending on the specific application.
What Screws Should You Use on Aluminum?
For aluminum, self-tapping screws or machine screws are commonly used. These screws create their own threads in the aluminum, reducing the need for pre-drilled holes. Stainless steel screws are often used, but if avoiding corrosion is a priority, consider screws with a corrosion-resistant coating or anodized aluminum screws.
Best Self-Tapping Screws for Aluminum
The best self-tapping screws for aluminum are made from stainless steel or coated materials to ensure they resist corrosion. For high-performance applications, 316 stainless steel screws are a top choice. They are strong, durable, and resistant to corrosion, making them ideal for use with aluminum.
What Metal Won’t Corrode with Aluminum?
When choosing fasteners that will work alongside aluminum without causing corrosion, titanium is an excellent choice. Titanium is highly resistant to corrosion and is compatible with aluminum. Another good option is bronze, which can also resist corrosion and is often used in marine applications alongside aluminum.
Summary
When selecting bolts for aluminum, stainless steel remains a popular choice due to its strength and durability, despite the risk of galvanic corrosion. However, understanding and addressing galvanic corrosion risks and exploring alternative materials can help achieve the best outcomes for your aluminum structures.
Choosing the right bolt for your project is crucial for ensuring both performance and safety. If you’re unsure which one to select, feel free to contact us for expert advice. We’re here to help you make the best decision for your needs.
Hengrui fastener company is specializing in the manufacturing and exporting of bolts, screws, nuts, washers, and custom non-standard fastener, with many different materials, like carbon steel, stainless steel, brass, aluminum, titanium, special alloy steel, etc.