When it comes to precision engineering, manufacturing, or construction, the fasteners we use are more important than they might seem at first glance. Custom bolts are crucial to making sure that the things we make, things we build, and the products we use go together strongly, reliably, and for a long time. Unlike off-the-shelf bolts, custom bolts are designed to fit our specific project needs and provide us with much better answers for combinations of strength and compatibility.
What is a Custom Bolt Manufacturer?
A custom bolt manufacturer is a company that specializes in producing bolts tailored to meet the precise specifications of a project. These bolts differ from standard, mass-produced bolts by offering modifications in size, material, shape, and finish. With 15 years of experience in the fastener industry, we supply high-quality products for many industries like automotive, machinery, wind energy, and more. We work with different materials such as carbon steel, stainless steel, brass, titanium, and special alloy steels.
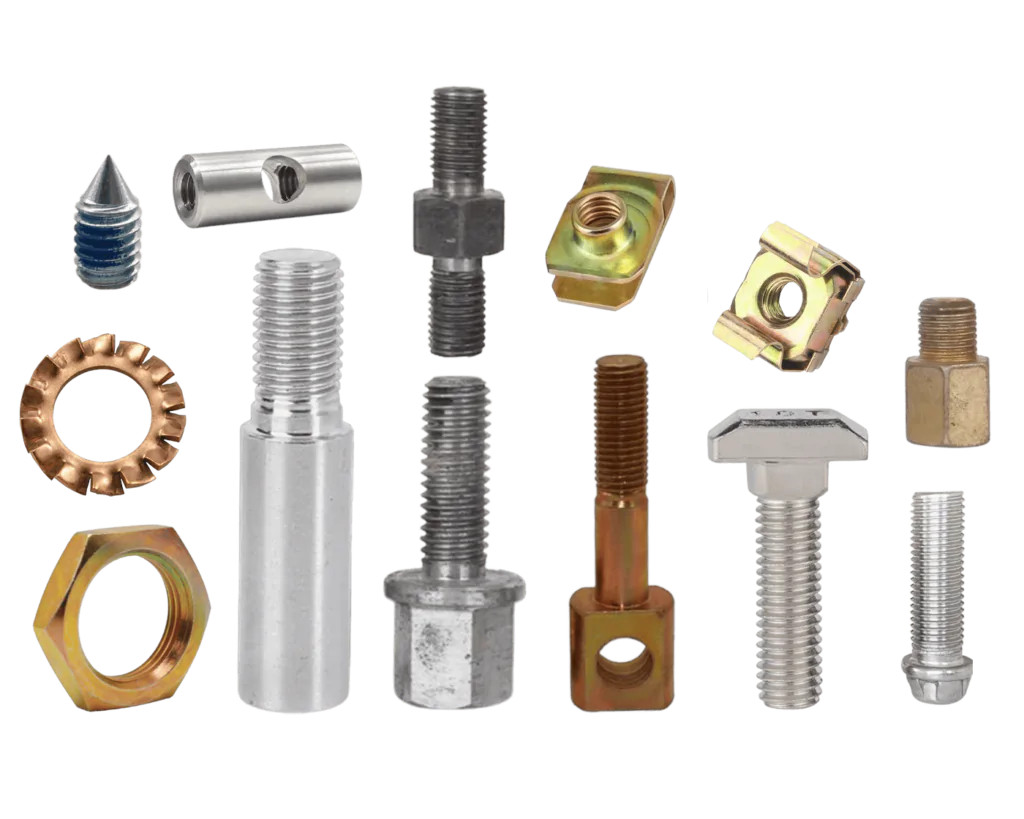
Custom bolt manufacturing is a complex and detailed process that involves several key steps and decisions. Let’s take a closer look at what makes these bolts unique and how they’re crafted to perfection.
What Materials Can Custom Bolts Be Made From?
One of the major advantages of custom bolts is the flexibility in material selection. Custom bolts can be made from various materials to ensure the correct balance of strength, durability, and corrosion resistance for different industries. Some common materials include:
- Carbon Steel – A popular choice for high strength and cost-effectiveness. It is ideal for applications where the bolt needs to withstand heavy mechanical stress.
- Alloy Steel – Often used for more demanding applications, alloy steel bolts provide enhanced strength and wear resistance, making them suitable for heavy machinery and high-pressure environments.
- Stainless Steel – Known for its corrosion resistance, stainless steel is the go-to material for applications in corrosive environments, such as marine, food processing, or chemical industries.
- Titanium – Highly resistant to corrosion and known for its lightweight properties, titanium is often used in aerospace and military applications.
- Brass – Known for its aesthetic appeal and corrosion resistance, brass bolts are commonly used in electrical and decorative applications.
- Exotic Alloys – For specialized applications, manufacturers can use exotic alloys like A286 or other high-performance metals that can withstand extreme temperatures and environments.
By selecting the right material, custom bolt manufacturers ensure that the bolts meet specific strength, temperature, and corrosion resistance needs for each project.
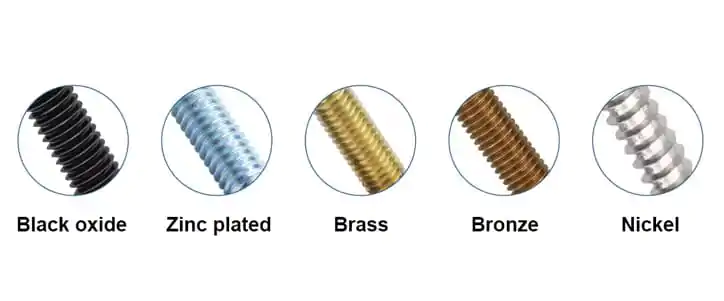
What Manufacturing Processes Are Used to Create Custom Bolts?
The manufacturing process is a key element in producing custom bolts that meet high standards of quality and precision. Depending on the project requirements, several methods are used to shape and form bolts:
- The manufacturing process is a key element in producing custom bolts that meet high standards of quality and precision. Depending on the project requirements, several methods are used to shape and form bolts:
- Forging – The process of shaping metal using localized compressive forces. Forging results in bolts with excellent mechanical properties, making them ideal for heavy-duty applications.
- Machining – For bolts with highly precise dimensions, machining is used to cut away material to the desired shape.
- Heat Treatment – Bolts may undergo heat treatment to enhance their hardness and strength, which is essential for high-stress environments.
- Cutting and Turning – These processes are used to create bolts of specific lengths and shapes, ensuring they fit precisely into the components they will secure.
- Milling, Drilling, and Threading – These techniques are essential for creating detailed bolt features like grooves, holes, or threads that allow the bolts to perform specific functions.
- Laser Cutting – Precision laser cutting allows for incredibly detailed and accurate cuts, which is especially useful when working with thin or hard-to-machine materials.
- Surface Grinding and Finishing – To ensure the bolt has a smooth and polished surface, which is vital for reducing friction and preventing corrosion, manufacturers use surface grinding and finishing techniques.
These various manufacturing processes, combined with strict quality control procedures, ensure that each custom bolt meets the required specifications for strength, performance, and durability.

How Do Custom Bolts Ensure Project Compatibility?
By tailoring each bolt to specific project requirements, custom bolt manufacturers ensure that bolts fit perfectly, reduce compatibility issues, and improve overall performance. In industries like aerospace or automotive, where precision and reliability are paramount, custom bolts are essential for achieving a seamless fit and long-lasting results.
Custom bolts are designed with particular dimensions, threading types, and material properties to ensure compatibility with the other components they interact with. This means fewer issues related to loose or improperly fitting bolts, reducing downtime and maintenance costs.
What Industry Standards Do Custom Bolt Manufacturers Follow?
Custom bolt manufacturers often adhere to various industry standards to ensure that their products are safe, reliable, and compatible with other components. These standards serve as a benchmark for quality and performance. Some of the most common standards include:
- ANSI (American National Standards Institute)
- ASTM (American Society for Testing and Materials)
- DFAR (Defense Federal Acquisition Regulation)
- DIN (Deutsches Institut für Normung)
- ISO (International Organization for Standardization)
- RoHS (Restriction of Hazardous Substances)
By meeting these industry standards, custom bolt manufacturers guarantee that their products are compliant with the necessary regulations and can be used in highly regulated industries like aerospace, defense, and electronics.
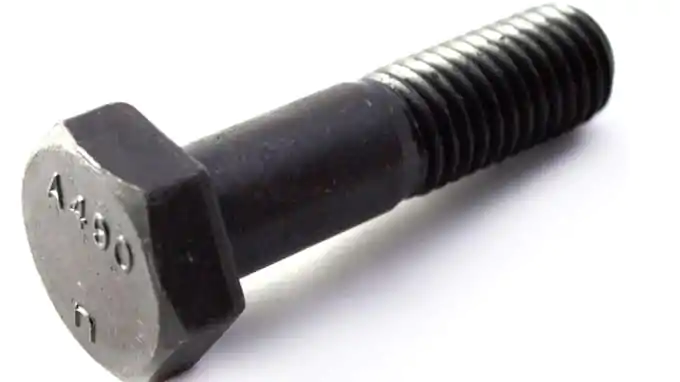
How Are Custom Bolts Finished for Durability and Corrosion Resistance?
After manufacturing, custom bolts often undergo finishing processes to improve their durability and appearance. Finishes can be applied to enhance corrosion resistance, improve aesthetics, or increase surface hardness. Some common finishes include:
- Zinc Coating – Provides corrosion resistance and is commonly used for outdoor applications.
- Anodizing – Enhances corrosion resistance and can also add color to the bolts, making them ideal for decorative or functional use in electronics and architectural projects.
- Cadmium Plating – Used for corrosion protection, particularly in harsh, high-temperature environments.
- Chrome Plating – A popular finish for aesthetic purposes and corrosion resistance in automotive and machinery applications.
- Powder Coating – Adds a durable and attractive finish, often used for bolts that need a protective coating in industrial and construction applications.
These finishing techniques not only improve the lifespan of bolts but also ensure they meet the aesthetic and performance requirements of each project.
Conclusion: The Importance of Custom Bolt Manufacturers
Custom bolts are a crucial part of many industries, offering precision, strength, and durability for specialized applications. Whether it’s the automotive sector, aerospace, or construction, custom bolt manufacturers provide tailored solutions that ensure the right fit and functionality for any project. From material selection to manufacturing processes, these manufacturers ensure that every bolt meets the highest standards of quality and performance.
By partnering with a custom bolt manufacturer, businesses can ensure that they get the exact fasteners they need, reducing waste, improving project timelines, and ultimately ensuring the success of their ventures.