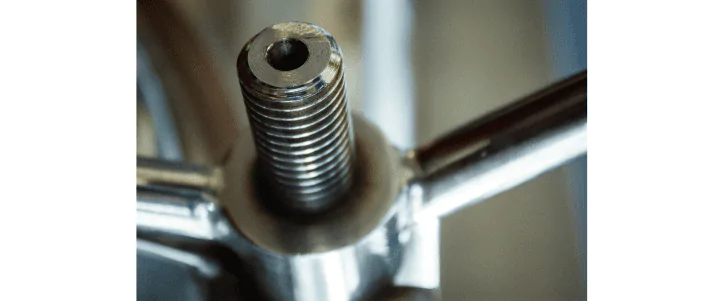
Fastener thread production is a critical manufacturing step that determines the performance and application range of the fastener. The two most common methods of producing fastener threads are: rolled threads vs cut threads. This article will detail the advantages and disadvantages of the two methods to help you quickly choose the process that’s right for you:
What are Rolled Threads?
Rolled threads are made by by high-pressure rolling of a cylindrical blank bolt between two molds containing the thread pattern, compacting the thread shape into the material to form the threads. This method does not remove any originasl material and increases the strength of the thread by compacting the steel’s grain structure, making it more durable and fatigue-resistant.
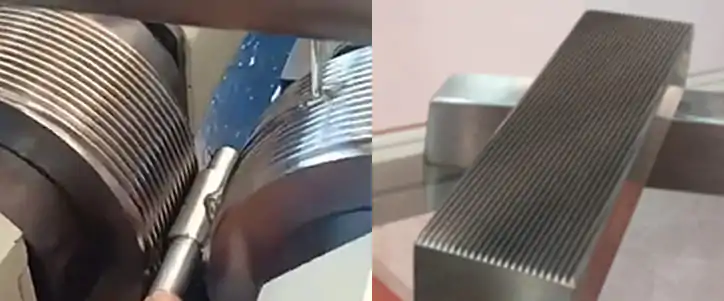
The advantages and disadvantages of thread rolling
Thread Rolling Advantages:
Enhanced strength and fatigue resistance: Due to the rearrangement of the metal grain structure along the thread shape, the tensile and fatigue strength, rolled threads bolt, rod are generally stronger than cut threads.
Good surface quality: The surface of the generated thread is smooth and burr-free, reducing the risk of cracks.
High efficiency and low cost: Rolled threads are a faster process than cut threading, and no material cutting is required, which reduces material costs and is suitable for large quantities of production.
Environmentally friendly: No chips are generated, reducing waste and disposal costs compared to thread cutting, making it more environmentally friendly.
Thread Rolling disadvantages:
Large equipment investment: Special rolling equipment is required.
Certain requirements on materials: It is not suitable for all types of materials, especially those with higher hardness or brittleness.
Rolling threads are widely used in the mass production of threads with high-performance requirements, such as in the automotive, aerospace, construction, and heavy machinery industries.
What are Cut Threads(Machined threads)?
Cut threads also called machined threads, are made by cutting material from a blank bolt or rod to form threads, this method is similar to engraving threads on a bolt. This is usually done using a cutting tool such as taps, dies, or thread milling cutter. Unlike rolling thread, cutting threads removes material from the fastener.
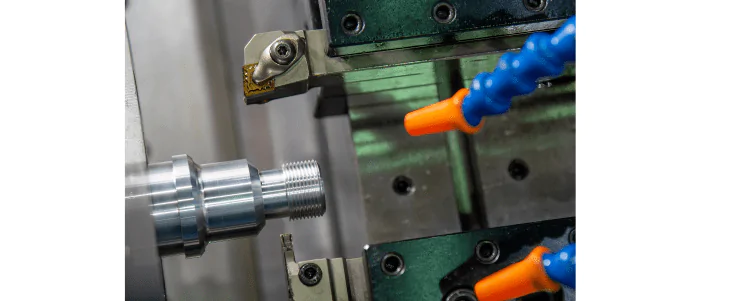
The advantages and disadvantages of thread cutting
Thread Cutting advantages:
- Wide applicability: Suitable for almost all types of materials, including those with high hardness and brittleness.
- High flexibility: Cut thread fasteners are easier to customize to unique specifications than roll threading, and can be easily adjusted and manufactured in different sizes and specifications, making them suitable for small-batch production and customization needs.
- Universal equipment: The equipment used, such as lathes and drilling machines etc., are suitable for a variety of machining tasks and do not require specialized equipment.
Thread Cutting disadvantages :
- Material waste: Chips will be generated during the cutting process, resulting in loss of raw materials.
- Slow production speed: Compared with rolling threads, the cutting threads speed is slow and not suitable for mass production.
- Surface quality: Burrs may be generated, requiring subsequent treatment to improve the surface quality of the threads.
Cut threads are suitable for small batch production, threads that require high precision and specific shapes, and bolt, bar or rod thread manufacturing of some brittle materials.
Rolled thread vs. Cut thread Fastener, Which One Should You Choose?
The choice of which thread manufacturing method to use depends mainly on the following factors:
Material Type: Assess whether the material can withstand the rolling process or whether it should be cut due to its characteristics. for example: Brittle materials, are not suitable for roll threading.
Production Volume: Rolled threads are mostly used for high-volume production, while cut threads can be used for small volumes or special requirements.
Cost and Efficiency: Evaluate the overall cost of the two processes, including equipment and operational costs, Rolled threads are generally being cheaper and more efficient.
Thread Requirements: Consider the specific requirements such as the complexity of the thread, tolerance grade, and the importance of strength and wear resistance. When there are special requirements for thread accuracy and shape, cutting may be required.
In summary, choosing between rolled or cut threads fasteners ultimately depends on your specific application needs, including considerations such as strength, material type and cost.
As a fastener supplier, Hengrui provides rolled and cut threaded fasteners, including various non-standard fasteners that can be customized to meet your specific requirements. If you’re still not sure which one to choose, contact us to discuss your application needs and our team will help you find the perfect fastener solution.