Stainless steel is a staple in various industries, but choosing the right type can be confusing. Are you struggling to decide between 18/8, 304, and 316 stainless steels for your project? Understanding their differences is crucial for ensuring durability and cost-effectiveness.
*18/8, 304, and 316 are all corrosion-resistan. but 316 stainless steels contains molybdenum, making it more corrosion-resistant than 18/8 and 304, especially in chloride-rich environments. 18/8 and 304 are similar and used interchangeably, good for general use and cost less, but 316 is stronger, more durable, and ideal for marine and highly corrosive applications.
Let’s dive into the world of 18/8, 304, and 316 stainless steels. What sets them apart? Which one is right for your project? Let’s find out!
What is 18/8 Stainless Steel?
18/8 stainless steel is a widely used type of austenitic stainless steel. The name “18/8” comes from its composition, which includes approximately 18% chromium and 8% nickel. This specific combination of chromium and nickel gives 18/8 stainless steel its unique properties and makes it a popular choice for various applications. These elements give 18/8 stainless steel its exceptional corrosion resistance and durability. Excellent corrosion resistance in mild environments, good weldability, and mechanical performance. It is non-magnetic but can become slightly magnetic when cold worked.
What Are the Advantages of 18/8 Stainless Steel?
18/8 stainless steel boasts several advantages:
- Corrosion Resistance: Its composition makes it resistant to corrosion, particularly in moist and lightly corrosive environments.
- Mechanical Performance: Offers high strength and toughness, ensuring reliability in various applications.
- Workability: Easy to machine, weld, and form, suitable for making complex parts.
- Non-Magnetic: In its annealed state, it is non-magnetic, ideal for applications requiring non-magnetic materials.
- Food Safety: Widely used in food processing due to its corrosion resistance and ease of cleaning.
- Cost-Effective: More affordable compared to higher-grade stainless steels like 316, while still providing good performance.
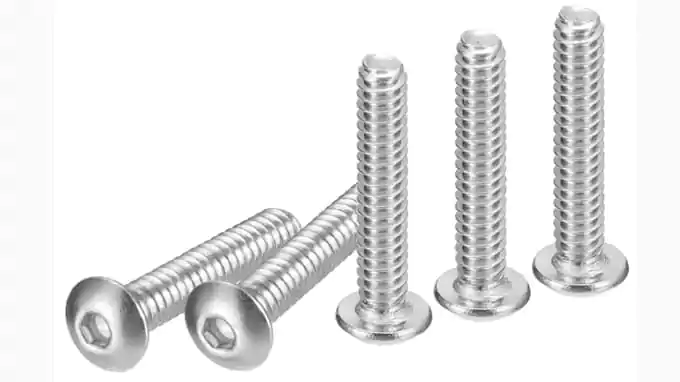
What Are the Disadvantages of 18/8 Stainless Steel?
While 18/8 stainless steel has many benefits, it also has some drawbacks:
- Chloride Corrosion: Not ideal for environments with high chloride concentrations, like seawater.
- High-Temperature Performance: Limited performance at sustained high temperatures above 800°C.
- Stress Corrosion Cracking: Susceptible to stress corrosion cracking in certain corrosive environments.
- Magnetic Changes: Can become slightly magnetic after cold working, which may be undesirable for some applications.
- Relatively Lower Strength: Compared to other stainless steels, such as martensitic grades.
- Price Fluctuations: The price can be affected by the market fluctuations of nickel.
Applications of 18/8 Stainless Steel?
18/8 stainless steel is versatile and widely used:
- Food Processing Equipment: Due to its corrosion resistance and ease of cleaning.
- Kitchenware: Commonly used for making cutlery, pots, and pans.
- Medical Devices: Utilized in medical instruments and equipment for its non-reactivity and sterilizability.
- General Industrial Uses: Employed in various industrial applications for its strength and durability.
- Building Materials: Used in construction for architectural elements and structural components.
- Automotive Industry: Components like exhaust systems and trims.
- Aerospace: Certain aerospace components.
- Household Appliances: Parts in dishwashers, refrigerators, and other appliances.
- Fasteners: Common material for bolts, nuts, and screws.
What is 316 Stainless Steel?
316 stainless steel is an austenitic alloy composed of 16-18% chromium, 10-14% nickel, and 2-3% molybdenum. Compared to 304 and 18/8 stainless steel, it with added molybdenum, enhancing its corrosion resistance, especially against chlorides and industrial chemicals. It has similar strength, toughness, and ductility but performs better in harsh environments and at low temperatures. Ideal for marine, chemical, and medical applications due to its high corrosion resistance.
What Are the Advantages of 316 Stainless Steel
316 stainless steel is highly valued for:
- Corrosion Resistance: Exceptional resistance to chlorides and aggressive chemicals.
- Mechanical Performance: High strength and toughness, even at low temperatures.
- High-Temperature Performance: Retains strength at elevated temperatures, up to 870°C intermittently and 925°C continuously.
- Workability: Easy to machine, form, and weld, especially the 316L variant.
- Non-Magnetic: Generally non-magnetic, suitable for sensitive applications.
- Sanitary Performance: Easy to clean and maintain, ideal for food and medical industries.
- Aesthetic Appeal: Its appearance is well-suited for architectural applications.
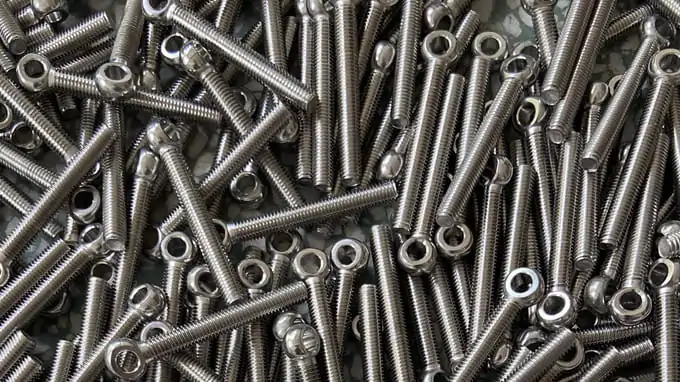
What Are the Disadvantages of 316 Stainless Steel
Despite its advantages, 316 stainless steel has some limitations:
- Cost: More expensive due to higher nickel and molybdenum content.
- Strength: While strong, its strength is lower than some other stainless steel types, like martensitic grades.
- Thermal Conductivity: Lower than carbon steel, which might be a drawback in certain applications.
- Machining Difficulty: Slightly harder to machine than other grades due to its toughness.
- Magnetic Issues: May become slightly magnetic after cold working.
- High-Temperature Limitations: Performance declines in temperatures exceeding 800°C.
- Stress Corrosion Cracking: Can occur in high-stress, corrosive environments.
Applications of 316 Stainless Steel
316 stainless steel’s superior properties make it ideal for:
- Chemical Processing Equipment: Withstands corrosive chemicals and solvents.
- Marine Applications: Perfect for ships, docks, and other marine environments.
- Medical Devices: Used in surgical instruments and implants due to its biocompatibility.
- Food Processing: Equipment and storage tanks due to its ease of cleaning.
- Architectural Applications: Decorative panels and structural components.
- Petrochemical Industry: Pipes, valves, and other components exposed to harsh chemicals.
- Marine Engineering: Equipment and structural components for marine environments.
What is 304 Stainless Steel?
304 stainless steel, also known as 18/8 stainless steel, is an austenitic alloy with 18-20% chromium and 8-10.5% nickel. It offers excellent corrosion resistance, high tensile strength, and good weldability. Compared to 316 stainless steel, 304 has slightly lower corrosion resistance but similar mechanical properties. Non-magnetic in its annealed state, it can become slightly magnetic when cold worked.
What Are the Advantages of 304 Stainless Steel
304 stainless steel is known for:
- Corrosion Resistance: Performs well in most general environments.
- Mechanical Properties: High strength and toughness.
- Workability: Easily welded and formed, suitable for various manufacturing processes.
- Cost-Effective: More affordable compared to 316 stainless steel, offering good performance at a lower cost.
- Sanitary Performance: Easy to clean, making it ideal for food and medical applications.
- Aesthetic Appeal: Its appearance is suitable for decorative uses.
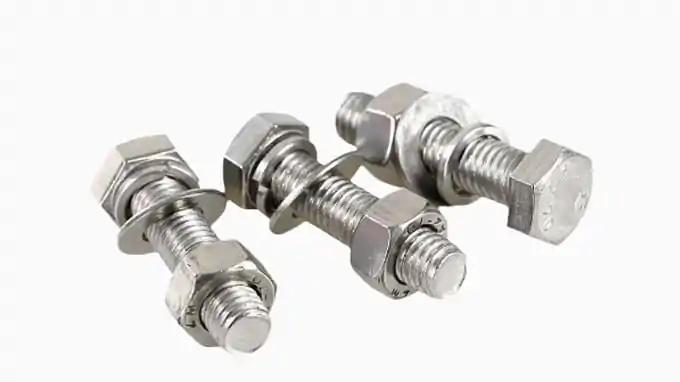
What Are the Disadvantages of 304 Stainless Steel
304 stainless steel also has some drawbacks:
- Chloride Corrosion: Less resistant to chloride-induced corrosion compared to 316 stainless steel.
- High-Temperature Performance: Limited performance in sustained high temperatures.
- Stress Corrosion Cracking: Can occur in certain environments.
- Magnetic Changes: Can become slightly magnetic after cold working.
- Cost Sensitivity: Price can fluctuate with the nickel market.
- Limited Chemical Resistance: Not suitable for extreme chemical environments.
Applications of 304 Stainless Steel
304 stainless steel’s versatility makes it suitable for many applications:
- Food Processing: Equipment and kitchenware.
- Architecture: Decorative panels and structural components.
- Medical Devices: Surgical instruments and medical equipment.
- Household Appliances: Parts in dishwashers, refrigerators, and other appliances.
- Industrial Equipment: Chemical and pharmaceutical processing equipment.
- Automotive: Exhaust systems and trims.
- Marine Engineering: Certain components in less aggressive marine environments.
How to Choose Between 18/8, 316, and 304 Stainless Steel Fasteners?
Choosing the right stainless steel fastener depends on several factors:
Application Environment
- General Environment: 18/8 or 304 stainless steel is usually sufficient.
- Marine or High-Corrosion Environment: 316 stainless steel is better due to its superior corrosion resistance.
Corrosion Resistance
- High Corrosion Resistance: 316 stainless steel is the best choice, especially in chloride-rich environments.
- General Corrosion Resistance: 304 and 18/8 stainless steel perform well in most environments.
Strength Requirements
- Higher Strength: 304 stainless steel typically offers higher strength.
- General Strength: 18/8 and 316 stainless steel provide adequate strength for most applications.
Cost Considerations
- Budget-Friendly: 18/8 stainless steel is the most economical.
- Mid-Range Cost: 304 stainless steel offers a good balance of cost and performance.
- Higher Budget: 316 stainless steel provides the best performance but at a higher cost.
Industry Requirements
- Food and Medical Industries: 304 stainless steel is often preferred.
- Chemical and Marine Industries: 316 stainless steel is necessary.
Temperature Conditions
- High-Temperature Environments: 316 stainless steel performs better under high temperatures.
Magnetic Requirements
- Non-Magnetic Applications: All three types are non-magnetic in the annealed state.
Availability
- Easily Available: 304 stainless steel is the most readily available.
- Specific Applications: 18/8 and 316 stainless steel are also widely available but may have fewer options.
Conclusion
Choosing the right stainless steel depends on your specific needs and application environment. For most general purposes, 18/8 or 304 stainless steel is suitable. For more demanding environments, particularly those involving corrosive substances or high temperatures, 316 stainless steel is the best choice. Always consult with a professional or supplier to ensure you select the most appropriate material for your project.
That’s it! If you have any more questions, Contact us at info@hrfastener.com or visit our website hrfastener.com.