Are you tired of your fasteners rusting away? Wondering which plating is the best for your needs? With my years of experience in the fastener industry, I’ll share the key differences, so you can make the best choice for your projects.
At Shanghai Hengrui Industry Co., Ltd., we specialize in providing top-quality nickel-plated fasteners to meet diverse customer needs.
What is nickel plated?
Nickel plating screw is a surface treatment that involves depositing a layer of nickel onto a screw, making it suitable for various applications. This is done through electroplating or electroless plating. The main objective is to improve the properties of the base metal, including its resistance to corrosion and wear.
Types of Nickel Plating
There are several types of nickel plating, each with its unique properties and applications:
- Electroless Nickel Plating: This method uses a chemical reaction to deposit nickel without an electric current. It provides a uniform coating and excellent wear resistance, making it ideal for complex shapes and high-precision components.
- Electrolytic Nickel Plating: This is the most common method, using an electric current to deposit nickel. It offers good corrosion resistance and a bright, attractive finish.
- Composite Nickel Plating: This technique incorporates other materials, such as phosphorus or boron, into the nickel layer to enhance specific properties like hardness or wear resistance.
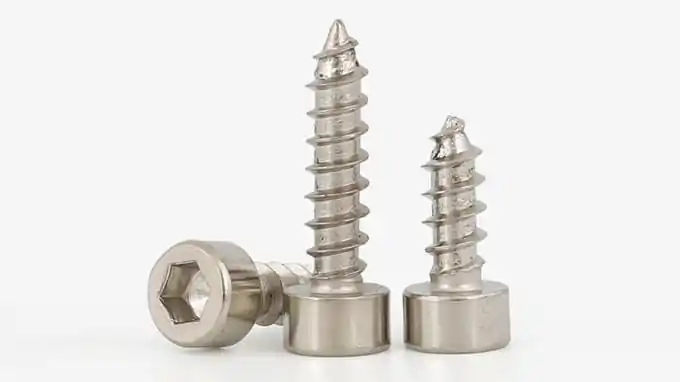
What is zinc plated?
A zinc plated screw is a type of fastener that has been coated with a layer of zinc to enhance its corrosion resistance and durability. This coating is typically applied through an electroplating process, although other methods like mechanical plating and hot-dip galvanizing are also used.
Types of Zinc Plating
- Electroplated Zinc: Uses an electrical current to deposit zinc onto the screw. It typically has a thickness of around 0.2 mm and is suitable for indoor use and applications where a shiny finish is desired.
- Hot-Dip Galvanized Zinc: Screws are dipped in molten zinc, resulting in a thicker coating of approximately 1.0 mm. This method is ideal for outdoor and structural applications due to its higher corrosion resistance.
- Mechanically Plated Zinc: Zinc powder is mechanically bonded to the screw, varying in thickness and used for screws that cannot withstand the heat of hot-dip galvanizing or the electrical current of electroplating.
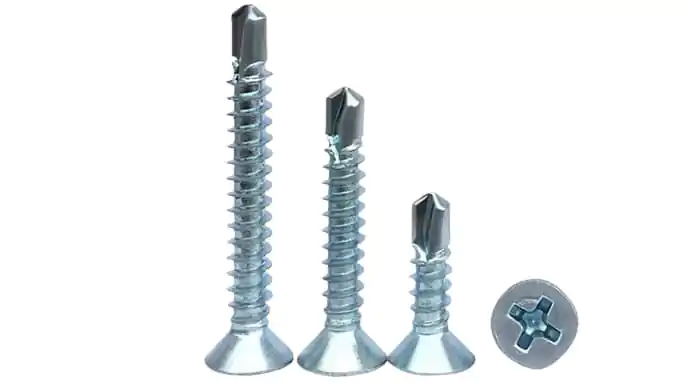
Nickel Plating vs. Zinc Plating Screw: What’s the Difference?
While both nickel and zinc plating are used to protect and enhance metal surfaces, they have distinct differences and applications.
- Corrosion Resistance: Zinc plating offers excellent corrosion resistance, especially in outdoor and high-humidity environments. Nickel plating also provides good corrosion resistance but is generally not as effective as zinc in harsh environments.
- Wear Resistance and Hardness: Nickel plating is known for excellent wear resistance and hardness, making it ideal for parts subjected to friction and abrasion. Zinc plating provides some wear resistance, but it is not as effective as nickel in this regard.
- Appearance: Zinc plating typically produces a brighter, more reflective finish, while nickel plating can provide a more subdued, satin-like finish.
- Cost: Zinc plating is generally less expensive than nickel plating.
- Applications: Zinc plating is commonly used in construction, electrical components, fasteners, hardware, and marine applications. Nickel plating is used in automotive, aerospace, electronics, medical, and military industries.
- Sacrificial Protection: Zinc plating acts as a sacrificial coating, protecting the underlying metal by corroding first. Nickel plating does not provide sacrificial protection.
- Substrate Compatibility: Zinc plating is ideal for iron and steel surfaces, whereas nickel plating is suitable for a wider range of materials, including steel and copper.
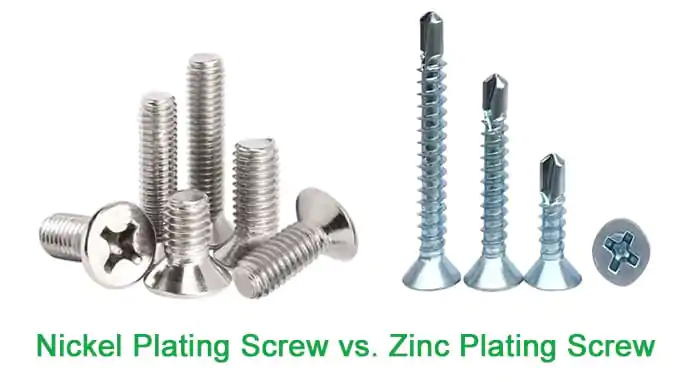
Main Benefits of Nickel Plating Screw
Nickel plating offers several benefits, making it a popular choice across various industries. Here are the primary advantages:
- Corrosion Resistance: Nickel acts as a barrier, protecting the base metal from oxidation and corrosion. This is particularly useful in harsh environments.
- Wear Resistance: The hardness of nickel enhances the durability and wear resistance of the coated object, extending its lifespan.
- Aesthetic Appeal: Nickel plating provides a bright, shiny finish that enhances the visual appeal of metal components.
- Electrical Conductivity: Nickel is an excellent conductor of electricity, making nickel-plated parts suitable for electronic applications.
- Smooth Finish: The plating process can create a uniform, smooth surface that fills in minor imperfections in the base metal.
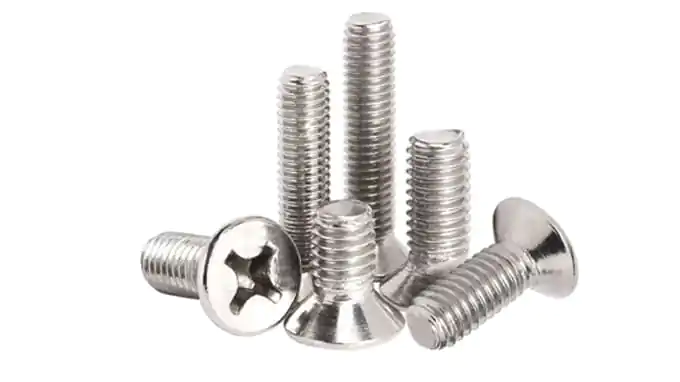
Main Benefits of Zinc Plating Screw
The main benefits of zinc plating are:
- Corrosion Resistance: Zinc plating provides a protective barrier that significantly slows down the corrosion process, making the screws suitable for various environments.
- Cost-Effective: Zinc plated screws are generally less expensive than stainless steel screws while still offering good corrosion resistance.
- Aesthetic Appeal: The shiny, smooth finish of zinc plated screws makes them visually appealing, especially for indoor applications.
- Versatility: Available in various types and sizes, making them suitable for a wide range of applications.
- Ease of Installation: The smooth surface of zinc plated screws reduces friction during installation, making them easier to drive into materials.
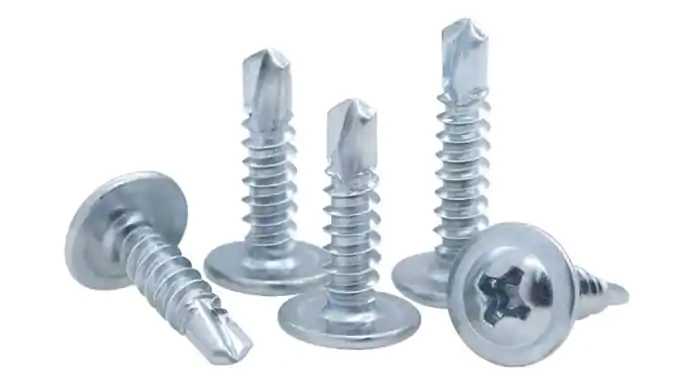
Applications of Nickel Plated Screw
Nickel-plated fasteners are used in a variety of applications due to their enhanced properties:
- Automotive and Aerospace Industries
- Electronics
- Furniture and Decorative Hardware
- Medical Devices
- Machinery Parts
Applications of Zinc Plated Screw
- Indoor Construction
- Furniture Assembly
- Automotive Industry
- Electronics
- General Purpose Fastening
Which One Should You Choose, Nickel or Zinc Plating Screw?
Choosing between nickel and zinc plating depends on your application’s specific requirements:
- Choose Zinc Plating if:
- Corrosion resistance in outdoor or high-humidity environments is a primary concern.
- Cost-effectiveness is an important factor.
- General-purpose applications require a bright, decorative finish.
- Choose Nickel Plating if:
- Wear resistance and hardness are crucial due to friction or abrasion.
- A durable, long-lasting, and aesthetically pleasing finish is needed.
- The application involves harsh environments requiring a more robust coating.
By considering these factors, you can select the most suitable plating method to ensure the longevity, performance, and appearance of your components.
Conclusion
The nickel plating process has a number of key benefits that make it an attractive option for improving the performance of metal parts. From resisting corrosion and withstanding wear to beautifying and providing electrical conductivity, nickel plated fasteners are an excellent choice for a number of different applications.
When deciding between nickel and zinc plating, carefully evaluate your specific needs and environmental conditions to choose the best solution for your project.
At Shanghai Hengrui Industry Co., Ltd, we pride ourselves on delivering top-quality nickel-plated and zinc-plated screws to meet your specific needs. contact us today or request a quote for pricing.